
联合国欧洲经济委员会(UNECE)条例No 16——关于批准以下的统一规定:I、用动力驱动车辆的安全带、约束系统、儿童约束系统和ISOFIX儿童约束系统;II、车辆的安全带、安全带提醒器、约束系统、儿童约束系统、ISOFIX儿童约束系统和i-Size儿童约束系统 [2018/629]
技术法规类型:欧盟Eurlex法规 来源:tbtmap
EURLEX ID:42018X0629
OJ编号:OJ L 109, 27.4.2018, p. 1–99
中文标题:联合国欧洲经济委员会(UNECE)条例No 16——关于批准以下的统一规定:I、用动力驱动车辆的安全带、约束系统、儿童约束系统和ISOFIX儿童约束系统;II、车辆的安全带、安全带提醒器、约束系统、儿童约束系统、ISOFIX儿童约束系统和i-Size儿童约束系统 [2018/629]
原文标题:Regulation No 16 of the Economic Commission for Europe of the United Nations (UNECE) — Uniform provisions concerning the approval of: I.Safety-belts, restraint systems, child restraint systems and ISOFIX child restraint systems for occupants of power-driven vehicles;II.Vehicles equipped with safety-belts, safety-belt reminders, restraint systems, child restraint systems, ISOFIX child restraint systems and i-Size child restraint systems [2018/629]
生效日期:2018-07-19
废止日期:9999-12-31
法规全文:查看欧盟官方文件
27.4.2018 |
EN |
Official Journal of the European Union |
L 109/1 |
Only the original UN/ECE texts have legal effect under international public law. The status and date of entry into force of this Regulation should be checked in the latest version of the UN/ECE status document TRANS/WP.29/343, available at:
http://www.unece.org/trans/main/wp29/wp29wgs/wp29gen/wp29fdocstts.html
Regulation No 16 of the Economic Commission for Europe of the United Nations (UNECE) — Uniform provisions concerning the approval of:
I. |
Safety-belts, restraint systems, child restraint systems and ISOFIX child restraint systems for occupants of power-driven vehicles; |
II. |
Vehicles equipped with safety-belts, safety-belt reminders, restraint systems, child restraint systems, ISOFIX child restraint systems and i-Size child restraint systems [2018/629] |
Incorporating all valid text up to:
Supplement 2 to the 07 series of amendments — Date of entry into force: 19 July 2018
CONTENTS
REGULATION
1. |
Scope |
2. |
Definitions |
3. |
Application for approval |
4. |
Markings |
5. |
Approval |
6. |
Specifications |
7. |
Tests |
8. |
Requirements concerning the installation in the vehicle |
9. |
Conformity of production |
10. |
Penalties for non-conformity of production |
11. |
Modifications and extension of approval of the vehicle type or safety-belt or restraint system type |
12. |
Production definitively discontinued |
13. |
Instructions |
14. |
Names and addresses of Technical Services responsible for conducting approval tests, and of Type Approval Authorities |
15. |
Transitional provisions |
ANNEXES
1A |
Communication concerning the approval or extension or refusal or withdrawal of approval or production definitively discontinued of a vehicle type with regard to safety-belt pursuant to Regulation No 16 |
1B |
Communication concerning the approval or extension or refusal or withdrawal of approval or production definitively discontinued of a type of safety-belt or restraint system for adult occupants of power-driven vehicles pursuant to Regulation No 16 |
2 |
Arrangements of the approval marks |
3 |
Diagram of an apparatus to test durability of retractor mechanism |
4 |
Diagram of an apparatus to test locking of emergency locking retractors |
5 |
Diagram of an apparatus for dust-resistance test |
6 |
Description of trolley, seat, anchorages and stopping device |
7 |
Description of manikin |
8 |
Description of curve of trolley's deceleration or acceleration as a function of time |
9 |
Instructions |
10 |
Dual buckle test |
11 |
Abrasion and micro-slip test |
12 |
Corrosion test |
13 |
Order of tests |
14 |
Control of conformity of production |
15 |
Procedure for determining the ‘H’ point and the actual torso angle for seating positions in motor vehicles |
16 |
Safety-belt installation showing the belt types and retractor types |
17 |
Requirements for the installation of safety-belts and restraint systems for adult occupants of power-driven vehicles on forward facing seats, for the installation of ISOFIX child restraint systems and i-Size child restraint systems |
18 |
Safety-belt reminder tests |
1. SCOPE
This Regulation applies to:
1.1. |
Vehicles of category M, N, O, L2, L4, L5, L6, L7 and T (1), with regard to the installation of safety-belts and restraint systems which are intended for separate use, i.e. as individual fittings, by persons of adult build occupying forward-facing, rearward-facing or side-facing seats; |
1.2. |
Safety-belts and restraint systems which are intended for separate use, i.e. as individual fittings, by persons of adult build occupying forward-facing, rearward-facing or side-facing seats, and are designed for installation in vehicles of category M, N, O, L2, L4, L5, L6, L7 and T (1); |
1.3. |
Vehicles of category M1 and N1 (1) with regard to the installation of child restraint systems, ISOFIX child restraint systems and i-Size child restraint systems; |
1.4. |
All seating positions in vehicle categories M and N fitted with safety belt with regard to safety belt reminder. |
1.5. |
At the request of the manufacturer, it also applies to the installation of child restraint systems and ISOFIX child restraint systems designated for installation in vehicles of categories M2 and M3 (1). |
1.6. |
At the request of the manufacturer, it also applies to safety-belts designated for installation on side-facing seats in vehicles of category M3 (Class II, III and B (1)). |
1.7. |
At the request of the manufacturer, it also applies to installing i-Size child restraint systems, in case i-Size seating positions are defined by the vehicle manufacturer. |
2. DEFINITIONS
2.1. Safety-belt (seat-belt, belt)
An arrangement of straps with a securing buckle, adjusting devices and attachments which is capable of being anchored to the interior of a power-driven vehicle and is designed to diminish the risk of injury to its wearer, in the event of collision or of abrupt deceleration of the vehicle, by limiting the mobility of the wearer's body. Such an arrangement is generally referred to as a ‘belt assembly’, which term also embraces any device for absorbing energy or for retracting the belt.
The arrangement can be tested and approved as a safety-belt arrangement or as a restraint system.
2.1.1. Lap belt
A two-point belt which passes across the front of the wearer's pelvic region.
2.1.2. Diagonal belt
A belt which passes diagonally across the front of the chest from the hip to the opposite shoulder.
2.1.3. Three-point belt
A belt which is essentially a combination of a lap strap and a diagonal strap.
2.1.4. S-type belt
A belt arrangement other than a three-point belt or a lap belt.
2.1.5. Harness belt
A S-type belt arrangement comprising a lap belt and shoulder straps; a harness belt may be provided with an additional crotch strap assembly.
2.2. Belt type
Belts of different ‘types’ are belts differing substantially from one another; the differences may relate in particular to:
2.2.1. |
Rigid parts (buckle, attachments, retractor, etc.); |
2.2.2. |
The material, weave, dimensions and colour of the straps; or |
2.2.3. |
The geometry of the belt assembly. |
2.3. Strap
A flexible component designed to hold the body and to transmit stresses to the belt anchorages.
2.4. Buckle
A quick-release device enabling the wearer to be held by the belt. The buckle may incorporate the adjusting device, except in the case of a harness belt buckle.
2.5. Belt adjusting device
A device enabling the belt to be adjusted according to the requirements of the individual wearer and to the position of the seat. The adjusting device may be part of the buckle, or a retractor, or any other part of the safety-belt.
2.6. Pre-loading device
An additional or integrated device which tightens the seat-belt webbing in order to reduce the slack of the belt during a crash sequence.
2.7. ‘Reference zone’ means the space between two vertical longitudinal planes, 400 mm apart and symmetrical with respect to the H-point, and defined by rotation from vertical to horizontal of the head-form apparatus, described in Regulation No 21 Annex 1. The apparatus shall be positioned as described in that annex to Regulation No 21 and set to the maximum length of 840 mm.
2.8. ‘Airbag assembly’ means a device installed to supplement safety-belts and restraint systems in power-driven vehicles, i.e. system which, in the event of a severe impact affecting the vehicle automatically deploys a flexible structure intended to limit, by compression of the gas contained within it, the gravity of the contacts of one or more parts of the body of an occupant of the vehicle with the interior of the passenger compartment. Any such described deployed structure shall not be considered as a rigid part.
2.9. ‘Passenger airbag’ means an airbag assembly intended to protect occupant(s) in seats other than the driver's in the event of a frontal collision.
2.10. ‘Child restraint’ means a safety device as defined in Regulation No 44 or Regulation No 129.
2.11. ‘Rearward-facing’ means facing in the direction opposite to the normal direction of travel of the vehicle.
2.12. Attachments
Parts of the belt assembly including the necessary securing components, which enable it to be attached to the belt anchorages.
2.13. Energy absorber
Device designed to disperse energy independently of or jointly with the strap and forming part of a belt assembly.
2.14. Retractor
Device to accommodate part or the whole of the strap of a safety-belt.
2.14.1. Non-locking retractor (type 1)
A retractor from which the strap is extracted to its full length by a small external force and which provides no adjustment for the length of the extracted strap.
2.14.2. Manually unlocking retractor (type 2)
A retractor requiring the manual operation of a device by the user to unlock the retractor in order to obtain the desired strap extraction and which locks automatically when the said operation ceases.
2.14.3. Automatically locking retractor (type 3)
A retractor allowing extraction of the strap to the desired length and which, when the buckle is fastened, automatically adjusts the strap to the wearer. Further extraction of the strap is prevented without voluntary intervention by the wearer.
2.14.4. Emergency locking retractor (type 4)
A retractor which during normal driving conditions does not restrict the freedom of movement by the wearer of the safety-belt. Such a device has length adjusting components which automatically adjust the strap to the wearer and a locking mechanism actuated in an emergency by:
2.14.4.1. |
Deceleration of the vehicle (single sensitivity), |
2.14.4.2. |
A combination of deceleration of the vehicle, movement of the webbing or any other automatic means (multiple sensitivity). |
2.14.5. Emergency locking retractor with higher response threshold (type 4N)
A retractor of the type defined in paragraph 2.14.4, but having special properties as regards its use in vehicles of categories M2, M3, N1, N2 and N3 (2).
2.14.6. Belt adjustment device for height
A device enabling the position in height of the upper pillar loop (directly connected to the vehicle or the rigid seat structure) of a belt to be adjusted according to the requirements of the individual wearer and the position of the seat. Such a device may be considered as a part of the belt or a part of the anchorage of the belt.
2.14.7. ‘Flexible shoulder adjustment device for height’
A device for adjusting to the shoulder height of the individual wearer, where the adjusting part is not directly attached to the vehicle construction (e.g. pillar) or the seat construction (e.g. the rigid seat structure), but where the adjusting of the shoulder part:
(a) |
Is realised via shifting over a flexible construction; and |
(b) |
Is not interfering the routing of the lap belt. |
2.15. Belt anchorages
Parts of the vehicles structure or seat structure or any other part of the vehicle to which the safety-belt assemblies are to be secured.
2.16. Vehicle type as regards safety-belts and restraint systems
Category of power-driven vehicles which do not differ in such essential respects as the dimensions, lines and materials of components of the vehicle structure or seat structure or any other part of the vehicle to which the safety-belts and the restraint systems are attached.
2.17. Restraint system
A system for a specific vehicle type or a type defined by the vehicle manufacturer and agreed by the Technical Service consisting of a seat and a belt fixed to the vehicle by appropriate means and consisting additionally of all elements which are provided to diminish the risk of injury to the wearer, in the event of an abrupt vehicle deceleration, by limiting the mobility of the wearer's body.
2.18. Seat
A structure which may or may not be integral with the vehicle structure complete with trim, intended to seat one adult person. The term covers both an individual seat or part of a bench seat intended to seat one person.
2.18.1. ‘A front passenger seat’ means any seat where the ‘foremost H-point’ of the seat in question is in or in front of the vertical transverse plane through the driver's R-point.
2.18.2. ‘Forward-facing seat’ means a seat which can be used while the vehicle is in motion and which faces towards the front of the vehicle in such a manner that the vertical plane of symmetry of the seat forms an angle of less than + 10° or – 10° with the vertical plane of symmetry of the vehicle.
2.18.3. ‘Rearward-facing seat’ means a seat which can be used while the vehicle is in motion and which faces towards the rear of the vehicle in such a manner that the vertical plane of symmetry of the seat forms an angle of less than + 10° or – 10° with the vertical plane of symmetry of the vehicle.
2.18.4. ‘Side-facing seat’ means a seat which can be used while the vehicle is in motion and which faces towards the side of the vehicle in such a manner that the vertical plane of symmetry of the seat forms an angle of 90° (± 10°) with the vertical plane of symmetry of the vehicle.
2.19. Group of seats
Either a bench-type seat or seats which are separate but side by side (i.e. fixed so that front seat anchorages of one of these seats are in line with the front or the rear anchorages of the other or between the anchorages of the other seat) and accommodate one or more seated adult persons.
2.20. Bench seat
A structure complete with trim, intended to seat more than one adult person.
2.21. Adjustment system of the seat
The complete device by which the seat or its parts can be adjusted to a position suited to the morphology of the seated occupant; this device may, in particular, permit of:
2.21.1. |
Longitudinal displacement; |
2.21.2. |
Vertical displacement; |
2.21.3. |
Angular displacement. |
2.22. Seat anchorage
The system by which the seat assembly is secured to the vehicle structure, including the affected parts of the vehicle structure.
2.23. Seat type
A category of seats which do not differ in such essential respects as:
2.23.1. |
The shape, dimensions and materials of the seat structure; |
2.23.2. |
The types and dimensions of the seat lock adjustment and locking systems; |
2.23.3. |
The type and dimensions of the belt anchorage on the seat, of the seat anchorage and of the affected parts of the vehicle structure. |
2.24. Displacement system of the seat
A device enabling the seat or one of its parts to be displaced angularly or longitudinally, without a fixed intermediate position (to facilitate access by passengers).
2.25. Locking system of the seat
A device ensuring that the seat and its parts are maintained in any position of use.
2.26. Enclosed buckle-release button
A buckle-release button such that it shall not be possible to release the buckle using a sphere having a diameter of 40 mm.
2.27. Non-enclosed buckle-release button
A buckle-release button such that it shall be possible to release the buckle using a sphere having a diameter of 40 mm.
2.28. Tension-reducing device
A device which is incorporated in the retractor and reduces the tension of the strap automatically when the safety-belt is fastened. When it is released, such a device switches off automatically.
2.29. ‘ISOFIX’ is a system for the connection of child restraint systems to vehicles which has two vehicle rigid anchorages, two corresponding rigid attachments on the child restraint system, and a mean to limit the pitch rotation of the child restraint system.
2.30. ‘ISOFIX child restraint system’ means a child restraint system, fulfilling the requirements of Regulation No 44 or Regulation No 129, which has to be attached to an ISOFIX anchorages system, fulfilling the requirements of Regulation No 14 or Regulation No 145.
2.31. ‘ISOFIX position’ means a system which allows installing:
(a) |
Either a universal ISOFIX forward facing child restraint system as defined in Regulation No 44; |
(b) |
Or a semi-universal ISOFIX forward facing child restraint system as defined in Regulation No 44; |
(c) |
Or a semi-universal ISOFIX rearward facing child restraint system as defined in Regulation No 44; |
(d) |
Or a semi-universal ISOFIX lateral facing position child restraint system as defined in Regulation No 44; |
(e) |
Or a specific vehicle ISOFIX child restraint system as defined in Regulation No 44; |
(f) |
Or an i-Size child restraint system as defined in Regulation No 129; |
(g) |
Or a specific vehicle ISOFIX child restraint system as defined in Regulation No 129. |
2.32. ‘ISOFIX Anchorages System’ means a system made up of two ISOFIX low anchorages, fulfilling the requirements of Regulation No 14 or Regulation No 145, and which is designed for attaching an ISOFIX child restraint system in conjunction with an anti-rotation device.
2.33. ‘ISOFIX low anchorage’ means one 6 mm diameter rigid round horizontal bar, extending from vehicle or seat structure to accept and restrain an ISOFIX child restraint system with ISOFIX attachments.
2.34. ‘Anti-rotation device’:
(a) |
An anti-rotation device for an ISOFIX universal child restraint system consists of the ISOFIX top-tether; |
(b) |
An anti-rotation device for an ISOFIX semi-universal child restraint system consists of a top tether, the vehicle dashboard or a support leg intended to limit the rotation of the restraint during a frontal impact; |
(c) |
An anti-rotation device for an i-Size child restraint system consists of either a top tether or a support leg, which is intended to limit the rotation of the restraint during a frontal impact; |
(d) |
For ISOFIX, i-Size, universal and semi-universal, child restraint systems the vehicle seat itself does not constitute an anti-rotation device. |
2.35. ‘ISOFIX Top Tether Anchorage’ means a feature, fulfilling the requirements of Regulation No 14 or Regulation No 145, such as a bar, located in a defined zone, designed to accept an ISOFIX top tether strap connector and transfer its restraint force to the vehicle structure.
2.36. A ‘guidance device’ is intended to help the person installing the ISOFIX child restraint system by physically guiding the ISOFIX attachments on the ISOFIX child restraint into correct alignment with the ISOFIX low anchorages to facilitate engagement.
2.37. ‘ISOFIX marking fixture’ means something that informs someone wishing to install an ISOFIX child restraint system of the ISOFIX positions in the vehicle and the position of each corresponding ISOFIX anchorages system.
2.38. ‘Child restraint fixture (CRF)’ means a fixture according to one of the ISOFIX fixtures defined in paragraph 4 of Annex 17 — Appendix 2 of this Regulation, and particularly whose dimensions are given from figure 1 to figure 8 in the previous mentioned paragraph 4. Those child restraint fixtures (CRF) are used, in this Regulation, to check which ISOFIX child restraint systems size envelopes classes mentioned in Regulation No 44 or in Regulation No 129 can be accommodated on the vehicle ISOFIX positions. Also one of the CRF, the so-called ISO/F2, which is described in figure 2 of the previous mentioned paragraph 4, is used in Regulation No 14 or Regulation No 145 to check the location and the possibility of access to any ISOFIX anchorages system.
Or a fixture, according to one of the two ‘booster seat’ fixtures defined in Annex 17, Appendix 5 of this Regulation, and particularly whose dimensions are given in figures 2 and 3 of Annex 17, Appendix 5. These fixtures are used, in this Regulation, to check which booster seat size envelopes mentioned in Regulation No 129 can be accommodated on vehicle seating positions, if any.
2.39. ‘i-Size support leg installation assessment volume’ means a volume, which ensures the dimensional and geometrical compatibility between the support leg of an i-Size child restraint system and an i-Size seating position of a vehicle.
2.40. ‘i-Size seating position’ means a seating position, if any defined by the vehicle manufacturer, which is designed to accommodate i-Size child restraint systems, as defined in Regulation No 129, and fulfils the requirements defined in this Regulation.
2.41. ‘Safety-belt reminder’, means a system dedicated to alert the driver when any of the occupants do not use the safety-belt. The system is constituted by a detection of an unfastened safety-belt and by two levels of driver's alert: a first level warning and a second level warning.
2.42. ‘Visual warning’ means a warning by visual signal (lighting, blinking or visual display of symbol or message).
2.43. ‘Audible warning’ means a warning by sound signal.
2.44. ‘First level warning’ means a visual warning activated when the ignition switch or master control switch is activated and any of the occupants' safety-belt is not fastened. An audible warning can be added as an option.
2.45. ‘Second level warning’ means a visual and audible warning activated when the vehicle is operated in accordance with paragraphs 8.4.2.4.1.1 to 8.4.2.4.1.3 with the safety-belt for any of the front row occupants being unfastened and the safety-belt for any of the rear row occupants either being or becoming unfastened.
2.46. ‘Safety-belt is not fastened’ means, at the option of the manufacturer, either the safety-belt buckle of any occupant is not engaged or the length of the pulled out webbing is less than the length of the webbing which is needed to buckle an un-occupied seat in the rearmost seating position.
2.47. ‘Vehicle is in normal operation’ means that vehicle is in forward motion at the speed greater than 10 km/h.
3. APPLICATION FOR APPROVAL
3.1. Vehicle type
3.1.1. The application for approval of a vehicle type with regard to the installation of its safety-belts and restraint systems shall be submitted by the vehicle manufacturer or by his duly accredited representative.
3.1.2. It shall be accompanied by the under mentioned documents in triplicate and the following particulars:
3.1.2.1. |
Drawings of the general vehicle structure on an appropriate scale, showing the positions of the safety-belts, and detailed drawings of the safety-belts and of the points to which they are attached; |
3.1.2.2. |
A specification of the materials used which may affect the strength of the safety-belts; |
3.1.2.3. |
A technical description of the safety-belts; |
3.1.2.4. |
In the case of safety-belts affixed to the seat structure; |
3.1.2.5. |
Detailed description of the vehicle type with regard to the design of the seats, of the seat anchorages and their adjustment and locking systems; |
3.1.2.6. |
Drawings, on an appropriate scale and in sufficient detail, of the seats, of their anchorages to the vehicle, and of their adjustment and locking systems; |
3.1.3. At the opinion of the manufacturer, a vehicle representative of the vehicle type to be approved or the parts of the vehicle considered essential for the safety-belt tests by the Technical Service conducting approval tests shall be submitted to the Service.
3.2. Safety-belt type
3.2.1. The application for approval of a type of safety-belt shall be submitted by the holder of the trade mark or by his duly accredited representative. In the case of restraint systems, the application for approval of a type of restraint system shall be submitted by the holder of the trade mark or by his representative or by the manufacturer of the vehicle in which it is to be installed or by his representative.
3.2.2. It shall be accompanied by:
3.2.2.1. |
A technical description of the belt type, specifying the straps and rigid parts used and accompanied by drawings of the parts making up the belt; the drawings shall show the position intended for the approval number and the additional symbol(s) in relation to the circle of the approval mark. The description shall mention the colour of the model submitted for approval, and specify the vehicle type(s) for which this belt type is intended. In the case of retractors, installation instructions for the sensing device shall be provided; and for pre-loading devices or systems a full technical description of the construction and function including the sensing, if any, describing the method of activation and any necessary method to avoid inadvertent activation shall be provided. In the case of a restraint system the description shall include: drawings of the vehicle structure and of the seat structure, adjustment system and attachments on an appropriate scale showing the sites of the seat anchorages and belt anchorages and reinforcements in sufficient detail; together with a specification of the materials used which may affect the strength of the seat anchorages and belt anchorages; and a technical description of the seat anchorages and the belts anchorages. If the belt is designed to be fixed to the vehicle structure through a belt adjustment device for height, the technical description shall specify whether or not this device is considered as a part of the belt; |
3.2.2.2. |
Six samples of the belt type, one of which is for reference purposes; |
3.2.2.3. |
A ten-metre length of each type of strap used in the type of belt; |
3.2.2.4. |
The Technical Service conducting the type-approval tests shall be entitled to request further samples. |
3.2.3. In the case of restraint systems, two samples which may include two of the samples of belts required under paragraphs 3.2.2.2 and 3.2.2.3 above at the option of the manufacturer, either a vehicle representative of the vehicle type to be approved, or the part or parts of the vehicle considered essential by the Technical Service conducting approval tests for testing the restraint system shall be submitted to the Service.
4. MARKINGS
The samples of a belt type or type of restraint system submitted for approval in conformity with the provisions of paragraphs 3.2.2.2, 3.2.2.3 and 3.2.2.4 above shall be clearly and indelibly marked with the manufacturer's name, initials or trade name or mark.
5. APPROVAL
5.1. A certificate conforming to the model specified in paragraphs 5.1.1 or 5.1.2 below shall be attached to the type approval certificate:
5.1.1. |
Annex 1A for applications referred to in paragraph 3.1; |
5.1.2. |
Annex 1B for applications referred to in paragraph 3.2; |
5.2. Vehicle type
5.2.1. If the vehicle submitted for approval pursuant this Regulation meets the requirements of paragraph 8 below, and of Annexes 15 and 16 to this Regulation, approval of that vehicle type shall be granted.
5.2.2. An approval number shall be assigned to each type approved. Its first two digits (at present 07 corresponding to the 07 series of amendments) shall indicate the series of amendments incorporating the most recent major technical amendments made to the Regulation at the time of issue of the approval. The same Contracting Party shall not assign the same number to another vehicle type as defined in paragraph 2.16 above.
5.2.3. Notice of approval or of extension or refusal or withdrawal of approval or production definitively discontinued of a vehicle type pursuant to this Regulation shall be communicated to the Parties to the 1958 Agreement which apply this Regulation by means of a form conforming to the model in Annex 1A to this Regulation.
5.2.4. There shall be affixed, conspicuously and in a readily accessible place specified on the approval form, to every vehicle conforming to a vehicle type approved under this Regulation an international approval mark consisting of:
5.2.4.1. |
A circle surrounding the letter ‘E’ followed by the distinguishing number of the country which has granted approval (3). |
5.2.4.2. |
The number of this Regulation, followed by the letter ‘R’, a dash and the approval number to the right of the circle prescribed in paragraph 5.2.4.1 above. |
5.2.5. If the vehicle conforms to a vehicle type approved, under one or more other Regulations annexed to the Agreement, in the country which has granted approval under this Regulation, the symbol prescribed in paragraph 5.2.4.1 need not be repeated; in such a case the additional numbers and symbols of all the Regulations under which approval has been granted in the country which has granted approval under this Regulation shall be placed in vertical columns to the right of the symbol prescribed in paragraph 5.2.4.1 above.
5.2.6. The approval mark shall be clearly legible and be indelible.
5.2.7. The approval mark shall be placed close to or on the vehicle data plate affixed by the manufacturer.
5.3. Safety-belt type
5.3.1. If the samples of a type of belt which are submitted in conformity with the provisions of paragraph 3.2 above meet the requirements of paragraphs 4, 5.3 and 6 of this Regulation, approval shall be granted.
5.3.2. An approval number shall be assigned to each type approved. Its first two digits (at present 06 corresponding to the 06 series of amendments) shall indicate the series of amendments incorporating the most recent major technical amendments made to the Regulation at the time of issue of the approval. The same Contracting Party may not assign the same number to another type of belt or restraint system.
5.3.3. Notice of approval or of extension or refusal of approval of a type of belt or restraint system, pursuant to this Regulation, shall be communicated to the Contracting Parties to the 1958 Agreement which apply this Regulation by means of a form conforming to the model in Annex 1B to this Regulation.
5.3.4. In addition to the marks prescribed in paragraph 4 above, the following particulars shall be affixed in a suitable space to every belt conforming to a type approved under this Regulation:
5.3.4.1. |
An international approval mark consisting of:
|
5.3.4.2. |
The following additional symbol(s):
|
5.3.5. Annex 2, paragraph 2 to this Regulation gives examples of arrangements of the approval mark.
5.3.6. The particulars referred to in paragraph 5.3.4 above shall be clearly legible and be indelible, and may be permanently affixed either by means of a label or by direct marking. The label or marking shall be resistant to wear.
5.3.7. The labels referred to in paragraph 5.3.6 above may be issued either by the Type Approval Authority which has granted the approval or, subject to that Authority's authorization, by the manufacturer.
6. SPECIFICATIONS
6.1. General specifications
6.1.1. Each sample submitted in conformity with paragraphs 3.2.2.2, 3.2.2.3 and 3.2.2.4 above shall meet the specifications set forth in paragraph 6 of this Regulation.
6.1.2. The belt or the restraint system shall be so designed and constructed that, when correctly installed and properly used by an occupant, its satisfactory operation is assured and it reduces the risk of bodily injury in the event of an accident.
6.1.3. The straps of the belt shall not be liable to assume a dangerous configuration.
6.1.4. The use of materials with properties of polyamide 6 as regards water retention is prohibited in all mechanical parts for which such a phenomenon is likely to have an adverse effect on their operation.
6.2. Rigid parts
6.2.1. General
6.2.1.1. The rigid parts of the safety-belt, such as buckles, adjusting devices, attachments and the like, shall not have sharp edges liable to cause wear or breakage of the straps by chafing.
6.2.1.2. All parts of the belt assembly liable to be affected by corrosion shall be suitably protected against it. After undergoing the corrosion test prescribed in paragraph 7.2 below, neither signs of deterioration likely to impair the proper functioning of the device nor any significant corrosion shall be visible to the unaided eye of a qualified observer.
6.2.1.3. Rigid parts intended to absorb energy or to be subjected to or to transmit a load shall not be fragile.
6.2.1.4. The rigid items and parts made of plastics of a safety-belt shall be so located and installed that they are not liable, during every day use of a power-driven vehicle, to become trapped under a moveable seat or in a door of that vehicle. If any of these items and parts do not comply with the above conditions, they shall be subjected to the cold impact test specified in paragraph 7.5.4 below. After the test, if any visible cracks are present in any plastic cover or retainer of rigid item, the complete plastic part shall then be removed and the remaining assembly shall then be assessed against its continued security. If the remaining assembly is still secure, or no visible cracks are present, it will then be further assessed against the test requirements specified in paragraphs 6.2.2, 6.2.3 and 6.4 below.
6.2.2. Buckle
6.2.2.1. The buckle shall be so designed as to preclude any possibility of incorrect use. This means, inter alia, that it shall not be possible for the buckle to be left in a partially-closed condition. The procedure for opening the buckle shall be evident. The parts of the buckle likely to contact the body of the wearer shall present a section of not less than 20 cm2 and at least 46 mm in width, measured in a plane situated at a maximal distance of 2,5 mm from the contact surface. In the case of harness belt buckles, the latter requirement shall be regarded as satisfied if the contact area of the buckle with the wearer's body is comprised between 20 and 40 cm2.
6.2.2.2. The buckle, even when not under tension, shall remain closed whatever the position of the vehicle. It shall not be possible to release the buckle inadvertently, accidentally or with a force of less than 1 daN. The buckle shall be easy to use and to grasp; when it is not under tension and when under the tension specified in paragraph 7.8.2 below, it shall be capable of being released by the wearer with a single simple movement of one hand in one direction; in addition, in the case of belt assemblies intended to be used for the front outboard seats, except in these harness belts, it shall also be capable of being engaged by the wearer with a simple movement of one hand in one direction. The buckle shall be released by pressing either a button or a similar device. The surface to which this pressure is applied shall have the following dimensions, with the button in the actual release position and when projected into a plane perpendicular to the button's initial direction of motion: for enclosed buttons, an area of not less than 4,5 cm2 and a width of not less than 15 mm; for non-enclosed buttons, an area of not less than 2,5 cm2 and a width of not less than 10 mm. The buckle release area shall be coloured red. No other part of the buckle shall be of this colour. When the seat is occupied, a red warning light as part of the buckle shall be permitted, if it is switched off by the action of buckling the seat belt. Lights illuminating the buckle in a colour other than red are not required to be switched off by the action of buckling the seat belt. These lights shall not illuminate the buckle in such a way that the perception of the red colour of the buckle release or the red of the warning light is affected.
6.2.2.3. The buckle, when tested in accordance with paragraph 7.5.3 below, shall operate normally.
6.2.2.4. The buckle shall be capable of withstanding repeated operation and, prior to the dynamic test specified in paragraph 7.7 below shall undergo 5 000 opening and closing cycles under normal conditions of use. In the case of harness belt buckles, this test may be carried out without all the tongues being introduced.
6.2.2.5. The force required to open the buckle in the test as prescribed in paragraph 7.8 below shall not exceed 6 daN.
6.2.2.6. The buckle shall be tested for strength as prescribed in paragraphs 7.5.1 and, where appropriate, 7.5.5 below. It shall not break, be seriously distorted or become detached under the tension set up by the prescribed load.
6.2.2.7. In the case of buckles which incorporate a component common to two assemblies, the strength and release tests of paragraphs 7.7 and 7.8 below shall also be carried out with the part of the buckle pertaining to one assembly being engaged in the mating part pertaining to the other, if it is possible for the buckle to be so assembled in use.
6.2.3. Belt adjusting device
6.2.3.1. The belt after being put on by the wearer, shall either adjust automatically to fit him or be such that the manually adjusting device shall be readily accessible to the seated wearer and shall be convenient and easy to use. It shall also allow the belt to be tightened with one hand to suit the wearer's body size and the position of the vehicle seat.
6.2.3.2. Two samples of each belt adjusting device shall be tested in accordance with the requirements of paragraph 7.3 below. The strap slip shall not exceed 25 mm for each sample of adjusting device and the sum of shifts for all the adjusting devices shall not exceed 40 mm.
6.2.3.3. All the adjustment devices shall be tested for strength as prescribed in paragraph 7.5.1 below. They shall not break or become detached under the tension set up by the prescribed load.
6.2.3.4. When tested in accordance with paragraph 7.5.6 below the force required to operate any manually adjusting device shall not exceed 5 daN.
6.2.4. Attachments and belt adjustment devices for height
The attachments shall be tested for strength as prescribed in paragraphs 7.5.1 and 7.5.2 below. The actual belt adjustment devices for height shall be tested for strength as prescribed in paragraph 7.5.2 of this Regulation where they have not been tested on the vehicle in application of Regulation No 14 (in its last version of amendments) relative to anchorages of safety-belts. These parts shall not break or become detached under the tension set up by the prescribed load.
6.2.5. Retractors
Retractors shall be subjected to tests and shall fulfil the requirements specified below, including the tests for strength prescribed in paragraphs 7.5.1 and 7.5.2 below. (These requirements are such that they exclude non-locking retractors.)
6.2.5.1. Manually unlocking retractors
6.2.5.1.1. The strap of a safety-belt assembly equipped with a manually unlocking retractor shall not move more than 25 mm between locking positions of the retractor.
6.2.5.1.2. The strap of a safety-belt assembly shall extract from a manually unlocking retractor within 6 mm of its maximum length when a tension of not less than 1,4 daN and not more than 2,2 daN is applied to the strap in the normal direction of pull.
6.2.5.1.3. The strap shall be withdrawn from the retractor and allowed to retract repeatedly by the method described in paragraph 7.6.1 until 5 000 cycles have been completed. The retractor shall then be subjected to the corrosion test given in paragraph 7.2 and to the dust test given in paragraph 7.6.3 below. It shall then satisfactorily complete a further 5 000 cycles of withdrawal and retraction. After the above tests, the retractor shall operate correctly and still meet the requirements of paragraphs 6.2.5.1.1 and 6.2.5.1.2 above.
6.2.5.2. Automatically locking retractors
6.2.5.2.1. The strap of a safety-belt assembly equipped with an automatically locking retractor shall not move more than 30 mm between locking positions of the retractor. After a rearward movement of the wearer, the belt shall either remain at its initial position or return to that position automatically on subsequent forward movements of the wearer.
6.2.5.2.2. If the retractor is part of a lap belt, the retracting force of the strap shall be not less than 0,7 daN when measured in the free length between the dummy and the retractor in accordance with paragraph 7.6.4 below.
If the retractor is part of an upper torso restraint, the retracting force of the strap shall be not less than 0,1 daN and not more than 0,7 daN when similarly measured.
6.2.5.2.3. The strap shall be withdrawn from the retractor and allowed to retract repeatedly by the method described in paragraph 7.6.1 until 5 000 cycles have been completed. The retractor shall then be subjected to the corrosion test given in paragraph 7.2 and after that to the dust test given in paragraph 7.6.3 below. It shall then satisfactorily complete a further 5 000 cycles of withdrawal and retraction. After the above tests the retractor shall operate correctly and still meet the requirements of paragraphs 6.2.5.2.1 and 6.2.5.2.2 above.
6.2.5.3. Emergency locking retractors
6.2.5.3.1. An emergency locking retractor, when tested in accordance with paragraph 7.6.2 below, shall satisfy the conditions below. In the case of a single sensitivity, according to paragraph 2.14.4.1 of this Regulation, only the specifications regarding deceleration of the vehicle are valid.
6.2.5.3.1.1. The locking shall have occurred when the deceleration of the vehicle reaches 0,45 g (5) in the case of type 4 or 0,85 g in the case of type 4N retractors.
6.2.5.3.1.2. It shall not lock for values of acceleration of the strap measured in the direction of the extraction of the strap of less than 0,8 g in the case of type 4 or less than 1,0 g in the case of type 4N retractors.
6.2.5.3.1.3. It shall not lock when its sensing device is tilted 12° or less in any direction from the installation position specified by its manufacturer.
6.2.5.3.1.4. It shall lock when its sensing device is tilted by more than 27° in the case of type 4 or 40° in the case of type 4N retractors in any direction from the installation position specified by its manufacturer.
6.2.5.3.1.5. In cases where the operation of a retractor depends on an external signal or power source, the design shall ensure that the retractor locks automatically upon failure or interruption of that signal or power source. However, this requirement need not be met in the case of a retractor with multiple sensitivities, provided only one sensitivity is dependent on an external signal or power source and the failure of the signal or power source is indicated to the driver by optical and/or acoustical means.
6.2.5.3.2. When tested in accordance with paragraph 7.6.2 below, an emergency locking retractor with multiple sensitivity, including strap sensitivity, shall comply with the specified requirements and also lock up when strap acceleration measured in the direction of unreeling is not less than 3,0 g.
6.2.5.3.3. In the case of the tests mentioned in paragraphs 6.2.5.3.1 and 6.2.5.3.2 above the amount of strap movement which may occur before the retractor locks shall not exceed 50 mm starting at the length given in paragraph 7.6.2.1. In the case of the test mentioned in paragraph 6.2.5.3.1.2 above locking shall not occur during the 50 mm of strap movement starting at the length given in paragraph 7.6.2.1 below.
6.2.5.3.4. If the retractor is part of a lap belt, the retracting force of the strap shall be not less than 0,7 daN when measured in the free length between the dummy and the retractor in accordance with paragraph 7.6.4.
If the retractor is part of an upper torso restraint, the retracting force of the strap shall be not less than 0,1 daN and not more than 0,7 daN when similarly measured, except for a belt equipped with a tension-reducing device, in which case the minimum retracting force may be reduced to 0,05 daN only when such a device is in operation mode. If the strap passes through a guide or pulley, the retracting force shall be measured in the free length between the dummy and the guide or pulley.
If the assembly incorporates a device that upon manual or automatic operation prevents the strap from being completely retracted, such a device shall not be operated when these requirements are assessed.
If the assembly incorporates a tension-reducing device, the retracting force of the strap described in the above shall be measured with the device in operation mode and non-operation mode when these requirements are assessed before and after durability tests according to paragraph 6.2.5.3.5 below.
6.2.5.3.5. The strap shall be withdrawn from the retractor and allowed to retract repeatedly by the method described in paragraph 7.6.1 until 40 000 cycles have been completed. The retractor shall then be subjected to the corrosion test given in paragraph 7.2 and after that to the dust test prescribed in paragraph 7.6.3 below. It shall then satisfactorily complete a further 5 000 cycles (making 45 000 in all).
If the assembly incorporates a tension-reducing device, the above tests shall be conducted on condition that the tension-reducing device is in operation mode and in non-operation mode.
After the above tests, the retractor shall operate correctly and still meet the requirements of paragraphs 6.2.5.3.1, 6.2.5.3.3 and 6.2.5.3.4 above.
6.2.5.4. Retractors shall fulfil, after durability test according to paragraph 6.2.5.3.5, and immediately after the retracting force measurement according to paragraph 6.2.5.3.4 above, all next two specifications:
6.2.5.4.1. |
When retractors except automatically locking retractors are tested according to paragraph 7.6.4.2 below, the retractors shall be able to avoid any slack between torso and belt, and, |
6.2.5.4.2. |
When the buckle is unlatched to release the tongue, the retractor alone shall be able to retract strap fully. |
6.2.6. Pre-loading device
6.2.6.1. After being submitted to corrosion testing in accordance with paragraph 7.2 below, the pre-loading device (including the impact sensor connected to the device by the original plugs but without any current passing through them) shall operate normally.
6.2.6.2. It shall be verified that inadvertent operation of the device does not involve any risk of bodily injury for wearer.
6.2.6.3. In the case of pyrotechnic pre-loading devices:
6.2.6.3.1. |
After being submitted to conditioning in accordance with paragraph 7.9.1 below, operation of the pre-loading device shall not have been activated by temperature and the device shall operate normally. |
6.2.6.3.2. |
Precautions shall be taken to prevent the hot gases expelled from igniting adjacent flammable materials. |
6.3. Straps
6.3.1. General
6.3.1.1. The characteristics of the straps shall be such as to ensure that their pressure on the wearer's body is distributed as evenly as possible over their width and that they do not twist even under tension. They shall have energy-absorbing and energy-dispersing capacities. The straps shall have finished selvages which shall not become unravelled in use.
6.3.1.2. The width of the strap under load of 980 daN + 100 - 0 daN shall be not less than 46 mm. This dimension shall be measured according to the test prescribed in paragraph 7.4.3 below, stopping the machine at the abovementioned load (6).
6.3.2. Strength after room-conditioning
In the case of the two strap samples conditioned in conformity with paragraph 7.4.1.1 the breaking load of the strap, determined as prescribed in paragraph 7.4.2 below, shall be not less than 1 470 daN. The difference between the breaking loads of the two samples shall not exceed 10 per cent of the greater of the breaking loads measured.
6.3.3. Strength after special conditioning
In the case of the two strap samples conditioned in conformity with one of the provisions of paragraph 7.4.1 (except 7.4.1.1) below, the breaking load of the strap shall be not less than 75 per cent of average of the loads determined in the test referred to in paragraph 6.3.2 and not less than 1 470 daN. The Technical Service conducting the tests may dispense with one or more of these tests if the composition of the material used or information already available renders the test or tests superfluous.
6.4. Belt assembly or restraint system
6.4.1. Dynamic test
6.4.1.1. The belt assembly or restraint system shall be subjected to a dynamic test in conformity with paragraph 7.7 below.
6.4.1.2. The dynamic test shall be performed on two belt assemblies which have not previously been under load, except in the case of belt assemblies forming part of restraint systems when the dynamic test shall be performed on the restraint systems intended for one group of seats which have not previously been under load. The buckles of the belt assemblies to be tested shall have met the requirements of paragraph 6.2.2.4 above. In the case of safety-belts with retractors, the retractor shall have been subjected to the dust resistance test laid down in paragraph 7.6.3; in addition, in the case of safety-belts or restraint systems equipped with a pre-loading device comprising pyrotechnic means, the device shall have been subjected to the conditioning specified in paragraph 7.9.1 below.
6.4.1.2.1. The belts shall have undergone the corrosion test described in paragraph 7.2, after which the buckles shall be subjected to 500 additional opening and closing cycles under normal conditions of use.
6.4.1.2.2. Safety-belts with retractors shall have been subjected either to the tests described in paragraph 6.2.5.2 or to those described in paragraph 6.2.5.3 above. If, however, a retractor has already been subjected to the corrosion test in accordance with the provisions of paragraph 6.4.1.2.1 above, this test need not be repeated.
6.4.1.2.3. In the case of a belt intended for use with a belt adjustment device for height, as defined in paragraph 2.14.6 above, the test shall be carried out with the device adjusted in the most unfavourable position(s) chosen by the Technical Service responsible for testing. However:
6.4.1.2.3.1. |
If the belt adjustment device for height is constituted by the belt anchorage, as approved in accordance with the provisions of Regulation No 14, the Technical Service responsible for testing may, at its discretion, apply the provisions of paragraph 7.7.1 below; |
6.4.1.2.3.2. |
If a flexible shoulder adjustment device for height is part of the belt, it shall be tested as a restraint system and the Technical Service responsible for testing shall apply the provisions under paragraph 7.7.1 that count for testing on the part of the vehicle structure to which the restraint system is normally fitted. |
6.4.1.2.4. In the case of safety-belt with a preloading device the minimum displacement specified in paragraph 6.4.1.3.2 below may be reduced by half. For the purpose of this test, the preloading device shall be in operation.
6.4.1.2.5. In the case of a safety-belt with tension-reducing device, it shall be subjected to a durability test with such a device in operation mode according to paragraph 6.2.5.3.5 before a dynamic test. The dynamic test shall then be conducted with the tension-reducing device in operation mode.
6.4.1.3. During this test, the following requirements shall be met:
6.4.1.3.1. No part of the belt assembly or a restraint system affecting the restraint of the occupant shall break and no buckles or locking system or displacement system shall release or unlock; and
6.4.1.3.2. The forward displacement of the manikin shall be between 80 and 200 mm at pelvic level in the case of lap belts. In the case of other types of belts, the forward displacement shall be between 80 and 200 mm at pelvic level and between 100 and 300 mm at chest level. In the case of a harness belt, the minimum displacements specified above may be reduced by half. These displacements are the displacements in relation to the measurement points shown in Annex 7, Figure 6 to this Regulation.
6.4.1.3.3. In the case of a safety-belt intended to be used in an outboard front seating position protected by an airbag in front of it, the displacement of the chest reference point may exceed that specified in paragraph 6.4.1.3.2 above if its speed at this value does not exceed 24 km/h.
6.4.1.3.4. In case of a seating position, other than the outboard front seating position, which is protected with an airbag in front of it, the displacement of the chest reference point may exceed that specified in paragraph 6.4.1.3.2 if its speed at this value does not exceed 24 km/h in tests performed with the airbag in a vehicle related environment, reflecting the vehicle coordinates of the airbag mounting and attachment points.
6.4.1.4. In the case of a restraint system:
6.4.1.4.1. The movement of the chest reference point may exceed that specified in paragraph 6.4.1.3.2 above if it can be shown either by calculation or a further test that no part of the torso or the head of the manikin used in the dynamic test would have come into contact with any forward rigid part of the vehicle other than:
6.4.1.4.1.1. |
In the case of the driver, contact of the chest with the steering assembly would be allowed, if the latter meets the requirements of Regulation No 12 and provided contact does not occur at a speed higher than 24 km/h. For this assessment the seat shall be considered to be in one of the positions specified in paragraph 7.7.1.5 below. |
6.4.1.4.1.2. |
In the case of any other occupant, contact of the head or of the chest with any rigid part of the vehicle in front of the manikin is not allowed. Additionally contact of the manikin's head with its knees is not allowed. For this assessment the seat of the tested manikin and, if applicable, the seat in front of the manikin shall be considered to be in the positions specified in paragraph 7.7.1.6 below. With the exception of the deployed structure of an airbag assembly defined in paragraph 2.8, non-rigid material of < 50 Shore A hardness may be removed in order to demonstrate that covered or padded rigid parts are not contacted by the head or the chest of the manikin during the test. |
6.4.1.4.2. In vehicles where such devices are used, the displacement and locking systems enabling the occupants of all seats to leave the vehicle shall still be operable by hand after the dynamic test.
6.4.1.5. By way of derogation, in case of a restraint system, the displacements may be greater than those specified in paragraph 6.4.1.3.2 in the case where the upper anchorage fitted to the seat profits from the derogation provided in paragraph 7.4 of Regulation No 14.
6.4.2. Strength after abrasion conditioning
6.4.2.1. For both samples conditioned in compliance with paragraph 7.4.1.6 below, the breaking strength shall be assessed as prescribed in paragraphs 7.4.2 and 7.5 below. It shall be at least equal to 75 per cent of the breaking strength average determined during tests on unabraded straps and not less than the minimum load specified for the item being tested. Difference between breaking strength of the two samples shall not exceed 20 per cent of the highest measured breaking strength. For type 1 and type 2 procedures, the breaking strength test shall be carried out on strap samples only (para. 7.4.2). For type 3 procedure, the breaking strength test shall be carried out on the strap in combination with the metal component involved (para. 7.5).
6.4.2.2. The parts of the belt assembly to be subjected to an abrasion procedure are given in the following table and the procedure types which may be appropriate for them are indicated by ‘x’. A new sample shall be used for each procedure.
|
Procedure 1 |
Procedure 2 |
Procedure 3 |
Attachment |
— |
— |
x |
Guide or Pulley |
— |
x |
— |
Buckle-loop |
— |
x |
x |
Adjusting device |
x |
— |
x |
Parts sewn to the strap |
— |
— |
x |
Flexible shoulder adjusting device for height |
x |
— |
— |
7. TESTS
7.1. Use of samples submitted for approval of a type of belt or restraint system (see Annex 13 to this Regulation)
7.1.1. Two belts or restraint systems are required for the buckle inspection, the low-temperature buckle test, the low-temperature test described in paragraph 7.5.4 below where necessary, the buckle durability test, the belt corrosion test, the retractor operating tests, the dynamic test and the buckle-opening test after the dynamic test. One of these two samples shall be used for the inspection of the belt or restraint system.
7.1.2. One belt or restraint system is required for the inspection of the buckle and the strength test on the buckle, the attachment mountings, the belt adjusting devices and, where necessary, the retractors.
7.1.3. Two belts or restraint systems are required for the inspection of the buckle, the micro-slip test and the abrasion test. The belt adjusting device operating test shall be conducted on one of these two samples.
7.1.4. The sample of strap shall be used for testing the breaking strength of the strap. Part of this sample shall be preserved so long as the approval remains valid.
7.2. Corrosion test
7.2.1. A complete safety-belt assembly shall be positioned in a test chamber as prescribed in Annex 12 to this Regulation. In the case of an assembly incorporating a retractor, the strap shall be unwound to full length less 300 ± 3 mm. Except for short interruptions that may be necessary, for example, to check and replenish the salt solution, the exposure test shall proceed continuously for a period of 50 hours.
7.2.2. On completion of the exposure test the assembly shall be gently washed, or dipped in clean running water with a temperature not higher than 38 °C to remove any salt deposit that may have formed and then allowed to dry at room temperature for 24 hours before inspection in accordance with paragraph 6.2.1.2 above.
7.3. Micro-slip test (see Annex 11, Figure 3, to this Regulation)
7.3.1. The samples to be submitted to the micro-slip test shall be kept for a minimum of 24 hours in an atmosphere having a temperature of 20 ± 5 °C and a relative humidity of 65 ± 5 per cent. The test shall be carried out at a temperature between 15 and 30 °C.
7.3.2. It shall be ensured that the free section of the adjusting device points either up or down on the test bench, as in the vehicle.
7.3.3. A 5 daN load shall be attached to the lower end of the section of strap. The other end shall be subjected to a back and forth motion, the total amplitude being 300 ± 20 mm (see figure).
7.3.4. If there is a free end serving as reserve strap, it shall in no way be fastened or clipped to the section under load.
7.3.5. It shall be ensured that on the test bench the strap, in the slack position, descends in a concave curve from the adjusting device, as in the vehicle. The 5 daN load applied on the test bench shall be guided vertically in such a way as to prevent the load swaying and the belt twisting. The attachment shall be fixed to the 5 daN load as in the vehicle.
7.3.6. Before the actual start of the test, a series of 20 cycles shall be completed so that the self-tightening system settles properly.
7.3.7. 1 000 cycles shall be completed at a frequency of 0,5 cycles per second, the total amplitude being 300 ± 20 mm. The 5 daN load shall be applied only during the time corresponding to a shift of 100 ± 20 mm for each half period.
7.4. Conditioning of straps and breaking-strength test (static)
7.4.1. Conditioning of straps for the breaking-strength test
Samples cut from the strap referred to in paragraph 3.2.2.3 above shall be conditioned as follows:
7.4.1.1. Temperature-conditioning and hygrometric
The strap shall be conditioned in accordance with ISO 139 (2005), using the standard atmosphere or the standard alternative atmosphere. If the test is not carried out immediately after conditioning, the specimen shall be placed in a hermetically-closed receptacle until the test begins. The breaking load shall be determined within 5 minutes after removal of the strap from the conditioning atmosphere or from the receptacle.
7.4.1.2. Light-conditioning
7.4.1.2.1. The provisions of Recommendation ISO 105-B02 (1994/Amd2:2000) shall apply. The strap shall be exposed to light for the time necessary to produce a contrast equal to Grade 4 on the grey scale on Standard Blue Dye No 7.
7.4.1.2.2. After exposure, the strap shall be conditioned as described under paragraph 7.4.1.1. If the test is not carried out immediately after conditioning the specimen shall be placed in a hermetically-closed receptacle until the test begins. The breaking load shall be determined within five minutes after removal of the strap from the conditioning installation.
7.4.1.3. Cold-conditioning
7.4.1.3.1. The strap shall be conditioned as described under paragraph 7.4.1.1 above.
7.4.1.3.2. The strap shall then be kept for one and a half hours on a plane surface in a low-temperature chamber in which the air temperature is – 30 ± 5 °C. It shall then be folded and the fold shall be loaded with a mass of 2 kg previously cooled to – 30 ± 5 °C. When the strap has been kept under load for 30 minutes in the same low-temperature chamber, the mass shall be removed and the breaking load shall be measured within 5 minutes after removal of the strap from the low-temperature chamber.
7.4.1.4. Heat-conditioning
7.4.1.4.1. The strap shall be kept for three hours in a heating cabinet in an atmosphere having a temperature of 60 ± 5 °C and a relative humidity of 65 ± 5 per cent.
7.4.1.4.2. The breaking load shall be determined within five minutes after removal of the strap from the heating cabinet.
7.4.1.5. Exposure to water
7.4.1.5.1. The strap shall be kept fully immersed for three hours in distilled water, at a temperature of 20 ± 5 °C, to which a trace of a wetting agent has been added. Any wetting agent suitable for the fibre under test may be used.
7.4.1.5.2. The breaking load shall be determined within 10 minutes after removal of the strap from the water.
7.4.1.6. Abrasion conditioning
7.4.1.6.1. The abrasion conditioning will be performed on every device in which the strap is in contact with a rigid part of the belt, with the exception of all adjusting devices where the micro-slip test (paragraph 7.3) shows that the strap slips by less than half the prescribed value, in which case, the procedure 1 abrasion conditioning (paragraph 7.4.1.6.4.1) will not be necessary. The setting on the conditioning device will approximately maintain the relative position of strap and contact area.
7.4.1.6.2. The samples shall be conditioned as described under paragraph 7.4.1.1. The ambient temperature during the abrasion procedure shall be between 15 and 30 °C.
7.4.1.6.3. In the table below are listed the general conditions for each abrasion procedure.
|
Load daN |
Frequency Hz |
Cycles numbers |
Shift mm |
Procedure 1 |
2,5 |
0,5 |
5 000 |
300 ± 20 |
Procedure 2 |
0,5 |
0,5 |
45 000 |
300 ± 20 |
Procedure 3 (*1) |
0 to 5 |
0,5 |
45 000 |
— |
The shift given in the fifth column of this table represents the amplitude of a back and forth motion applied to the strap.
7.4.1.6.4. Particular conditioning procedures
7.4.1.6.4.1. Procedure 1: for cases where the strap slides through an adjusting device.
A vertical steady load of 2,5 daN shall be maintained on one end of the strap — the other end of the strap shall be attached to a device giving the strap a horizontal back and forth motion.
The adjusting device shall be placed on the horizontal strap so that the strap remains under tension (see Annex 11, Figure 1, to this Regulation).
7.4.1.6.4.2. Procedure 2: for cases where the strap changes direction in passing through a rigid part.
During this test, the angles of the straps shall be maintained as shown in Annex 11, Figure 2, to this Regulation.
The steady load of 0,5 daN shall be maintained during the test.
For cases where the strap changes direction more than once in passing through a rigid part, the load of 0,5 daN may be increased so as to achieve the prescribed strap movement of 300 mm through that rigid part.
7.4.1.6.4.3. Procedure 3: for cases where the strap is fixed to a rigid part by sewing or similar means.
The total back and forth motion shall be 300 ± 20 mm but the 5 daN load shall only be applied during a shift of 100 ± 20 mm for each half period (see Annex 11, Figure 3, to this Regulation).
7.4.2. Test of breaking strength of strap (static test)
7.4.2.1. The test shall be carried out each time on two new samples of strap, of sufficient length, conditioned in conformity with the provisions of paragraph 7.4.1 above.
7.4.2.2. Each strap shall be gripped between the clamps of a tensile-testing machine. The clamps shall be so designed as to avoid breakage of the strap at or near them. The speed of traverse shall be about 100 mm/min. The free length of the specimen between the clamps of the machine at the start of the test shall be 200 mm ± 40 mm.
7.4.2.3. The tension shall be increased until the strap breaks, and the breaking load shall be noted.
7.4.2.4. If the strap slips or breaks at or within 10 mm of either of the clamps the test shall be invalid and a new test shall be carried out on another specimen.
7.4.3. Width under load
7.4.3.1. The test shall be carried out each time on two new samples of strap, of sufficient length conditioned in conformity with the provisions of paragraph 7.4.1 above.
7.4.3.2. Each strap shall be gripped between the clamps of a tensile-testing machine. The clamps shall be so designed as to avoid breaking of the strap at or near them. The speed of traverse shall be about 100 mm/min. The free length of the specimen between the clamps of the machine at the start of the test shall be 200 mm ± 40 mm.
7.4.3.3. When the load reaches 980 daN + 100 – 0 daN, the machine shall be stopped and the measurement shall be completed within 5 seconds. The test has to be performed separately from the tensile test.
7.5. Test of belt assembly components incorporating rigid parts
7.5.1. The buckle and the adjusting device shall be connected to the tensile-testing apparatus by the parts of the belt assembly to which they are normally attached, and the load shall then build up to 980 daN.
In the case of harness belts, the buckle shall be connected to the testing apparatus by the straps which are attached to the buckle and the tongue or two tongues located in an approximately symmetrical way to the geometric centre of the buckle. If the buckle, or the adjusting device, is part of the attachment or of the common part of a three-point belt, the buckle or adjusting device shall be tested with the attachment, in conformity with paragraph 7.5.2 below, except in the case of retractors having a pulley or strap guide at the upper belt anchorage, when the load will be 980 daN and the length of strap remaining wound on the reel shall be the length resulting from locking as close as possible to 450 mm from the end of the strap.
7.5.2. The attachments and any belt adjustment devices for height shall be tested in the manner indicated in paragraph 7.5.1 above, but the load shall be 1 470 daN and shall, subject to the provisions of the second sentence of paragraph 7.7.1 below, be applied in the least favourable conditions likely to occur in a vehicle in which the belt is correctly installed. In the case of retractors the test is performed with the strap completely unwound from the reel.
7.5.3. Two samples of the complete belt assembly shall be placed in a refrigerated cabinet at – 10 ± 1 °C for two hours. The mating parts of the buckle shall be coupled together manually immediately after being removed from the refrigerated cabinet.
7.5.4. Two samples of complete belt assembly shall be placed in a refrigerated cabinet at – 10 °C ± 1 °C for two hours. The rigid items and parts made of plastics under test shall then be laid in turn upon a flat rigid steel surface (which has been kept with the samples in the refrigerated cabinet) placed on the horizontal surface of a compact rigid block with a mass of at least 100 kg and within 30 seconds of being removed from the refrigerated cabinet, an 18 kg steel mass shall be allowed to fall under gravity through 300 mm on to the test sample. The impact face of the 18 kg mass shall take the form of a convex surface with a hardness of at least 45 HRC having a transverse radius of 10 mm and a longitudinal radius of 150 mm placed along the centre line of the mass. One test sample shall be tested with the axis of the curved bar in line with the strap and the other sample shall be tested at 90° to the strap.
7.5.5. Buckles having parts common to two safety-belts shall be loaded in such a way as to simulate the conditions of use in the vehicle with seats in the mid-position of their adjustment. A load of 1 470 daN shall be applied simultaneously to each strap. The direction of the application of load shall be established according to paragraph 7.7.1 below. A suitable device for the test is shown in Annex 10 to this Regulation.
7.5.6. When testing a manually adjusting device, the strap shall be drawn steadily through the adjusting device, having regard for the normal conditions of use, at a rate of approximately 100 mm/s and the maximum force measured to the nearest 0,1 daN after the first 25 mm of strap movement. The test shall be carried out in both directions of strap travel through the device, the strap being cycled 10 times prior to the measurement.
7.6. Additional tests for safety-belts with retractors
7.6.1. Durability of retractor mechanism
7.6.1.1. The strap shall be withdrawn and allowed to retract for the required number of cycles at a rate of not more than 30 cycles per minute. In the case of emergency locking retractors, a snatch to lock the retractor shall be introduced at each fifth cycle.
The snatches shall occur in equal numbers at each of five different extractions, namely, 90, 80, 75, 70 and 65 per cent of the total length of the strap remaining wound on the retractor. However, where more than 900 mm is provided the above percentages shall be related to the final 900 mm of strap which can be withdrawn from the retractor.
7.6.1.2. A suitable apparatus for the tests specified in paragraph 7.6.1.1 above is shown in Annex 3 to this Regulation.
7.6.2. Locking of emergency locking retractors
7.6.2.1. The retractor shall be tested once for locking when the strap has been unwound to full length less 300 ± 3 mm.
7.6.2.1.1. In the case of a retractor actuated by strap movement, the extraction shall be in the direction in which it normally occurs when the retractor is installed in a vehicle.
7.6.2.1.2. When retractors are being tested for sensitivity to vehicle deceleration they shall be tested at the above extraction along two perpendicular axes, which are horizontal if the retractor is installed in a vehicle as specified by the safety-belt manufacturer. When this position is not specified, the testing authority shall consult the safety-belt manufacturer. One of these axes shall be in the direction chosen by the Technical Service conducting the approval test to give the most adverse conditions with respect to actuation of the locking mechanism.
7.6.2.2. A suitable apparatus for the tests specified in paragraph 7.6.2.1 above is described in Annex 4 to this Regulation. The design of any such test apparatus shall ensure that the required acceleration is given before the webbing is withdrawn out of the retractor by more than 5 mm and that the withdrawal takes place at an average rate of increase of acceleration of at least 55 g/s (7) and not more than 150 g/s in testing sensitivity for strap movement and of at least 25 g/s and not more than 150 g/s in testing sensitivity for vehicle deceleration.
7.6.2.3. To check conformity with the requirements of paragraphs 6.2.5.3.1.3 and 6.2.5.3.1.4, the retractor shall be mounted on a horizontal table and the table tilted with a speed not exceeding 2° per second until locking has occurred. The test shall be repeated with tilting in other directions to ensure that the requirements are fulfilled.
7.6.3. Dust resistance
7.6.3.1. The retractor shall be positioned in a test chamber as described in Annex 5 to this Regulation. It shall be mounted in an orientation similar to that in which it is mounted in the vehicle. The test chamber shall contain dust as specified in paragraph 7.6.3.2 below. A length of 500 mm of the strap shall be extracted from the retractor and kept extracted, except that it shall be subjected to 10 complete cycles of retraction and withdrawal within one or two minutes after each agitation of the dust. For a period of five hours, the dust shall be agitated every 20 minutes for five seconds by compressed air free of oil and moisture at a gauge pressure of 5,5 · 105 ± 0,5 · 105 Pa entering through an orifice, 1,5 ± 0,1 mm in diameter.
7.6.3.2. The dust used in the test described in paragraph 7.6.3.1 above shall consist of about 1 kg of dry quartz. The particle size distribution is as follows:
(a) |
Passing 150 μm aperture, 104 μm wire diameter: 99 to 100 per cent; |
(b) |
Passing 105 μm aperture, 64 μm wire diameter: 76 to 86 per cent; |
(c) |
Passing 75 μm aperture, 52 μm wire diameter: 60 to 70 per cent. |
7.6.4. Retracting forces
7.6.4.1. The retracting force shall be measured with the safety-belt assembly fitted to a dummy as for the dynamic test prescribed in paragraph 7.7 below. The strap tension shall be measured at the point of contact with (but just clear of) the dummy while the strap is being retracted at the approximate rate of 0,6 m/min. In the case of a safety-belt with tension-reducing device, the retracting force and strap tension shall be measured with the tension-reducing device in both operation mode and non-operation mode.
7.6.4.2. Before the dynamic test described in paragraph 7.7 below, the seated dummy, which is clothed with a cotton shirt, shall be tilted frontward until 350 mm of the strap is withdrawn from retractor, and then released to the initial position.
7.7. Dynamic test of belt assembly or of the restraint system
7.7.1. The belt assembly shall be mounted on a trolley equipped with the seat and the general anchorages as defined in Annex 6, Figure 1, to this Regulation. However, if the belt assembly is intended for a specific vehicle or for specific types of vehicle, the distances between the manikin and the anchorages shall be determined by the Technical Service conducting the tests, either in conformity with the instructions for fitting supplied with the belt or in conformity with the data supplied by the manufacturer of the vehicle. If the belt is equipped with a belt adjustment device for height such as defined in paragraph 2.14.6 above, the position of the device and the means of securing it shall be the same as those of the vehicle design.
In that case, when the dynamic test has been carried out for a type of vehicle it need not be repeated for other types of vehicle where each anchorage point is less than 50 mm distant from the corresponding anchorage point of the tested belt. Alternatively, manufacturers may determine hypothetical anchorage positions for testing in order to enclose the maximum number of real anchorage points.
7.7.1.1. In the case of a safety-belt or restraint system forming part of an assembly for which type approval is requested as a restraint system, the safety-belt shall be mounted either as defined in paragraph 7.7.1 or on the part of the vehicle structure to which the restraint system is normally fitted and this part shall be rigidly attached to the test trolley in the way prescribed in paragraphs 7.7.1.2 to 7.7.1.6 below.
In the case of a safety-belt or restraint system with pre-loading devices relying on component parts other than those incorporated in the belt assembly itself, the belt assembly shall be mounted in conjunction with the necessary additional vehicle parts on the test trolley in the manner prescribed in paragraphs 7.7.1.2 to 7.7.1.6 below.
Alternatively, in the case where those devices cannot be tested on the test trolley, the manufacturer may demonstrate by a conventional frontal impact test at 50 km/h in conformity with the procedure ISO 3560 (1975) that the device complies with the requirements of the Regulation.
7.7.1.2. The method used to secure the vehicle during the test shall not be such as to strengthen the anchorages of the seats or safety-belts or to lessen the normal deformation of the structure. No forward part of the vehicle shall be present which by limiting the forward movement of the manikin excepting the foot, would reduce the load imposed on the restraint system during the test. The parts of the structure eliminated can be replaced by parts of equivalent strength provided they do not hinder the forward movement of the manikin.
7.7.1.3. A securing device shall be regarded as satisfactory if it produces no effect on an area extending over the whole width of the structure and if the vehicle or the structure is blocked or fixed in front at a distance of not less than 500 mm from the anchorage of the restraint system. At the rear the structure shall be secured at a sufficient distance rearwards of the anchorages to ensure that the requirements of paragraph 7.7.1.2 above are fulfilled.
7.7.1.4. The seats of the vehicle shall be fitted and shall be placed in the position for driving use chosen by the Technical Service conducting approval tests to give the most adverse conditions with respect to strength, compatible with installing the manikin in the vehicle. The positions of the seats shall be stated in the report. The seat back, if adjustable for inclination, shall be locked as specified by the manufacturer or, in the absence of any specification, to an actual seat back angle as near as possible to 25° in the case of vehicles of categories M1 and N1 as near as possible to 15° in the case of vehicles of all other categories.
7.7.1.5. For the assessment of the requirements in paragraphs 6.4.1.4.1 and 6.4.1.4.1.1 the seat shall be positioned in its most forward driving position appropriate to the dimensions of the manikin.
7.7.1.6. For the assessment of the requirements in paragraphs 6.4.1.4.1 and 6.4.1.4.1.2 the seat adjustment shall be:
7.7.1.6.1. |
For front passenger seats: the occupant in the front shall be in its most forward travelling position according to the dimensions of the manikin. The positions of the seats shall be stated in the report. |
7.7.1.6.2. |
For rear seats: For any testing position of rear seated occupants, the position of the tested seating position, shall be considered as positioned to the seats R-Point. If the seat back is adjustable, the seat back angle should be adjusted using the 3-D H Point machine with its torso angle as close as possible to 10°. The seating position in front of the tested seating position shall be adjusted to the middle position of travel and height or in the nearest locking position thereto. If the seat back of this seat is adjustable, the seat back angle should be adjusted using the 3-D H Point machine with its torso angle as close as possible to 10°. This may be proven by a contour on CAD or drawing of the in-vehicle situation. |
7.7.1.7. Alternatively to paragraphs 7.7.1.5 and 7.7.1.6, in the case where those devices cannot be tested on the test trolley, the manufacturer may demonstrate by a conventional frontal impact test at 50 km/h in conformity with the procedure ISO 3560:2013 that the device complies with the requirements of this Regulation.
7.7.1.8. All the seats of any group of seats shall be tested simultaneously.
7.7.1.9. The dynamic tests of the harness belt system shall be carried out without the crotch strap (assembly), if there is any.
7.7.2. The belt assembly shall be attached to the manikin in Annex 7 to this Regulation as follows: a board 25 mm thick shall be placed between the back of the manikin and the seat back. The belt shall be firmly adjusted to the manikin. The board shall then be removed so that the entire length of its back is in contact with the seat back. A check shall be made to ensure that the mode of engagement of the two parts of the buckle entails no risk of reducing the reliability of locking.
7.7.3. The free ends of the straps shall extend sufficiently far beyond the adjusting devices to allow for slip.
7.7.4. Deceleration or acceleration devices
The applicant shall choose to use one of the two following devices:
7.7.4.1. Deceleration test device
The trolley shall be so propelled that at the moment of impact its free running speed is 50 km/h ± 1 km/h and the manikin remains stable. The stopping distance of the trolley shall be 40 cm ± 5 cm. The trolley shall remain horizontal throughout deceleration. The deceleration of the trolley shall be achieved by using the apparatus described in Annex 6 to this Regulation or any other device giving equivalent results. This apparatus shall comply with the performance hereafter specified:
The deceleration curve of the trolley, weighted with inert mass to produce a total mass of 455 kg ± 20 kg for safety-belt tests and 910 kg ± 40 kg for restraining systems tests where the nominal mass of the trolley and vehicle structure is 800 kg, shall remain within the hatched area of the graph in Annex 8. If necessary, the nominal mass of the trolley and attached vehicle structure can be increased by increments of 200 kg, in which case, an additional inert mass of 28 kg per increment shall be added. In no case shall the total mass of the trolley and vehicle structure and inert masses differ from the nominal value for calibration tests by more than ±40 kg. During calibration of the stopping device, the speed of the trolley shall be 50 km/h ± 1 km/h and the stopping distance shall be of 40 cm ± 2 cm.
7.7.4.2. Acceleration test device
The trolley shall be so propelled that its total velocity change ΔV is 51 km/h km/h. The trolley shall remain horizontal during the acceleration. The acceleration of the trolley shall be achieved by using the apparatus complying with the performance hereafter specified:
The acceleration curve of the trolley, weighted with inert mass, shall remain within the hatched area of the graph in Annex 8, and stay above the segment defined by the coordinates 10 g, 5 ms and 20 g, 10 ms. The start of the impact (T0) is defined, according to ISO 17 373 (2005) for a level of acceleration of 0,5 g. In no case shall the total mass of the trolley and vehicle structure and inert masses differ from the nominal value for calibration tests by more than ± 40 kg. During calibration of the acceleration test device, trolley's total velocity change ΔV shall be 51 km/h km/h.
Despite the fulfilment of the above requirements, the Technical Service shall use a mass of trolley (equipped with its seats), as specified in paragraph 1 of Annex 6, greater than 380 kg.
7.7.5. The trolley speed immediately before impact (only for deceleration trolleys, needed for stopping distance calculation), the trolley acceleration or deceleration, the forward displacement of the manikin and the speed of the chest at a 300 mm displacement of the chest shall be measured.
The velocity change will be calculated by integration of the recorded trolley acceleration or deceleration.
The distance to achieve the first 50 km/h km/h of the velocity change of the trolley may be calculated by double integration of the recorded trolley deceleration.
7.7.6. After impact, the belt assembly or restraint system and its rigid parts shall be inspected visually, without opening the buckle, to determine whether there has been any failure or breakage. In the case of restraint systems it shall also be ascertained, after the test, whether the parts of the vehicle structure which are attached to the trolley have undergone any visible permanent deformation. If there is any such deformation this shall be taken into account in any calculation made in accordance with paragraph 6.4.1.4.1 above.
7.7.7. However, if the tests were performed at a higher speed and/or the acceleration curve has exceeded the upper level of the hatched area and the safety belt meets the requirements, the test shall be considered satisfactory.
7.8. Buckle-opening test
7.8.1. For this test, belt assemblies or restraint devices which have already undergone the dynamic test in conformity with paragraph 7.7 above shall be used.
7.8.2. The belt assembly shall be removed from the test trolley without the buckle being opened. A load shall be applied to the buckle by direct traction via the straps tied to it so that all the straps are subjected to the force of daN. (It is understood that n is the number of straps linked to the buckle when it is in a locked position.) In the case where the buckle is connected to a rigid part, the load shall be applied at the same angle as the one formed by the buckle and the rigid end during the dynamic test. A load shall be applied at a speed of 400 ± 20 mm/min to the geometric centre of the buckle-release button along a fixed axis running parallel to the initial direction of motion of the button. During the application of the force needed to open the buckle, the buckle shall be held by a rigid support. The load quoted above shall not exceed the limit indicated in paragraph 6.2.2.5 above. The point of contact of the test equipment shall be spherical in form with a radius of 2,5 mm ± 0,1 mm. It shall have a polished metal surface.
7.8.3. The buckle-opening force shall be measured and any failure of the buckle noted.
7.8.4. After the buckle-opening test, the components of the belt assembly or of the restraint device which have undergone the tests prescribed in paragraph 7.7 above shall be inspected and the extent of the damage sustained by the belt assembly or restraint device during the dynamic test shall be recorded in the test report.
7.9. Additional tests on safety-belts with pre-loading devices
7.9.1. Conditioning
The pre-loading device may be separated from the safety-belt to be tested and kept for 24 hours at a temperature of 60 ± 5 °C. The temperature shall then be raised to 100 ± 5 °C for two hours. Subsequently it shall be kept for 24 hours at a temperature of – 30 ± 5 °C. After being removed from conditioning, the device shall warm up to ambient temperature. If it has been separated it shall be fitted again to the safety-belt.
7.10. Test report
7.10.1. The test report shall record the results of all the tests in paragraph 7 above and in particular:
(a) |
The type of device used for the test (acceleration or deceleration device); |
(b) |
The total velocity change; |
(c) |
The trolley speed immediately before impact only for deceleration trolleys; |
(d) |
The acceleration or deceleration curve during all the velocity change of the trolley; |
(e) |
The maximum forward displacement of the manikin; |
(f) |
The place — if it can be varied — occupied by the buckle during the test; |
(g) |
The buckle-opening force; |
(h) |
Any failure or breakage; |
(i) |
For any restraint system other than the driver the contour of the contact should be evaluated versus the movement of the manikin in the sled by the technical service in this report. |
If by virtue of paragraph 7.7.1 the anchorages prescribed in Annex 6 to this Regulation have not been respected, the test report shall describe how the belt assembly or the restraint system was installed and shall specify important angles and dimensions.
8. REQUIREMENTS CONCERNING THE INSTALLATION IN THE VEHICLE
8.1. Safety-belt and restraint systems equipment
8.1.1. With the exception of seating intended solely for use when the vehicle is stationary, the seats of vehicles of categories M1, M2 (of Class III or B (8)), M3 (of Class III or B) and N shall be equipped with safety-belts or restraint systems which satisfy the requirements of this Regulation.
Contracting Parties applying this Regulation may demand the installation of safety belts on M2 and M3 vehicles belonging to Class II.
When fitted, the safety belts and/or restraint systems in Class I, II or A vehicles belonging to category M2 or M3 have to be in compliance with the requirements of this Regulation.
Contracting Parties may, under national law, allow the installation of safety belts or restraint systems other than those covered by this Regulation provided that they are intended for disabled people.
Restraint systems complying with the provisions of Annex 8 of the 02 series of amendments to Regulation No 107 are exempted from the provisions of this Regulation.
Class I, or A vehicles belonging to category M2 or M3 may be fitted with safety belts and/or restraint systems conforming to the requirements of this Regulation.
Only vehicles belonging to category M2 or M3 may be fitted with restraint systems comprising a flexible shoulder adjustment device for height (paragraph 2.14.7).
8.1.2. The types of safety-belts or restraint systems for each seating position where installation is required shall be those specified in Annex 16 (with which neither non-locking retractors (para. 2.14.1) nor manually unlocking retractor (para. 2.14.2) can be used). For all seating positions where lap belts type B are specified in Annex 16 lap belts type Br3 are permitted except in the case that, in use, they retract to such an extent as to reduce comfort in a notable way after normal buckling up.
8.1.2.1. However, for outboard seating positions, other than front, of vehicles of the category N1 shown in Annex 16 and marked with the symbol Ø, the installation of a lap belt of type Br4m or Br4Nm is allowed, where there exists a passage between a seat and the nearest side wall of the vehicle intended to permit access of passengers to other parts of the vehicle. A space between a seat and the side wall is considered as a passage, if the distance between that side wall, with all doors closed, and a vertical longitudinal plane passing through the centre line of the seat concerned — measured at the R-point position and perpendicularly to the median longitudinal plane of the vehicle — is more than 500 mm.
8.1.3. Where no safety-belts are required any type of safety-belt or restraint system conforming to this Regulation may be provided at the choice of the manufacturer. A-type belts of the types permitted in Annex 16 may be provided as an alternative to lap belts for those seating positions where lap belts are specified in Annex 16.
8.1.4. On three point belts fitted with retractors, one retractor shall operate at least on the diagonal strap.
8.1.5. Except for vehicles of category M1 an emergency locking retractor of type 4N (para. 2.14.5) may be permitted instead of a retractor of type 4 (para. 2.14.4) where it has been shown to the satisfaction of the services responsible for the tests that the fitting of a type 4 retractor would not be practical.
8.1.6. For the front outboard and the front centre seating positions shown in Annex 16 and marked with the symbol *, lap belts of the type specified on that annex shall be considered adequate where the windscreen is located outside the reference zone defined in Annex 1 to Regulation No 21.
As regards safety-belts, the windscreen is considered as part of the reference zone when it is capable of entering into static contact with the test apparatus according to the method described in Annex 1 of Regulation No 21.
8.1.7. Every seating position in Annex 16 marked with the symbol ߦ, three-point belts of a type specified in Annex 16 shall be provided unless one of the following conditions is fulfilled, in which case two-point belts of a type specified in Annex 16 may be provided.
8.1.7.1. There is a seat or other vehicle parts conforming to paragraph 3.5 of Appendix 1 to Regulation No 80 directly in front, or
8.1.7.2. No part of the vehicle is in or, when the vehicle is in motion, capable of being in the reference zone, or
8.1.7.3. Parts of the vehicle within the said reference zone comply with the energy absorbing requirements set out in Appendix 6 of Regulation No 80.
8.1.8. Every passenger seating position which is fitted with a frontal protection airbag shall be provided with a warning against the use of a rearward-facing child restraint in that seating position. As a minimum, this information shall consist of a label containing clear warning pictograms as indicated below:
The overall dimensions shall be at least 120 × 60 mm or the equivalent area.
The label shown above may be adapted in such a way that the layout differs from the example above; however, the content shall meet the above prescriptions.
8.1.9. In the case of a frontal protection airbag in the front passenger seat, the warning shall be durably affixed to each face of the passenger front sun visor in such a position that at least one warning on the sun visor is visible at all times, irrespective of the position of the sun visor. Alternatively, one warning shall be located on the visible face of the stowed sun visor and a second warning shall be located on the roof behind the visor, so, at least one warning is visible all times. It shall not be possible to easily remove the warning label from the visor and the roof without any obvious and clearly visible damage remaining to the visor or the roof in the interior of the vehicle.
If the vehicle does not have a sun visor or roof, the warning label shall be positioned in a location where it is clearly visible at all times.
In the case of a frontal protection airbag for other seats in the vehicle, the warning shall be directly ahead of the relevant seat, and clearly visible at all times to someone installing a rear-facing child restraint on that seat. The requirements of this paragraph and paragraph 8.1.8 do not apply to those seating positions equipped with a device which automatically deactivates the frontal protection airbag assembly when any rearward facing child restraint is installed.
8.1.10. Detailed information, making reference to the warning, shall be contained in the owner's manual of the vehicle; as a minimum, the following text in all official languages of the country or countries where the vehicle could reasonably be expected to be registered (e.g. within the territory of the European Union, in Japan, in Russian Federation or in New Zealand, etc.), shall at least include:
‘NEVER use a rearward facing child restraint on a seat protected by an ACTIVE AIRBAG in front of it, DEATH or SERIOUS INJURY to the CHILD can occur’
The text shall be accompanied by an illustration of the warning label as found in the vehicle. The information shall be easily found in the owner's manual (e.g. specific reference to the information printed on the first page, identifying page tab or separate booklet, etc.).
The requirements of this paragraph do not apply to vehicles of which all passenger seating positions are equipped with a device which automatically deactivates the frontal protection airbag assembly when any rearward facing child restraint is installed.
8.1.11. In the case of seats capable of being turned to or placed in other orientations, designed for use when the vehicle is stationary, the requirements of paragraph 8.1.1 above shall only apply to those orientations designated for normal use when the vehicle is travelling on a road, in accordance with this Regulation.
8.2. General requirements
8.2.1. Safety-belts, restraint systems, and ISOFIX child restraint systems, as well as i-Size child restraint systems according to Annex 17 — Appendix 3, shall be fixed to anchorages and in case of i-Size child restraint systems, supported by a vehicle floor contact surface, conforming to the specifications of Regulation No 14 or Regulation No 145, such as the design and dimensional characteristics, the number of anchorages, and the strength requirements.
8.2.2. The safety-belts, restraint systems and child restraint systems recommended by the manufacturer according to Annex 17 —Appendix 3, shall be so installed that they will work satisfactorily and reduce the risk of bodily injury in the event of an accident. In particular, they shall be so installed that:
8.2.2.1. |
The straps are not liable to assume a dangerous configuration; |
8.2.2.2. |
The danger of a correctly positioned belt slipping from the shoulder of a wearer as a result of his/her forward movement is reduced to a minimum. |
8.2.2.3. |
The risk of the strap deteriorating through contact with sharp parts of the vehicle or seat structure, and child restraint systems recommended by the manufacturer according to Annex 17 — Appendix 3, is reduced to a minimum. |
8.2.2.4. |
The design and installation of every safety-belt provided for each seating position shall be such as to be readily available for use. Furthermore, where the complete seat or the seat cushion and/or the seat back can be folded to permit access to rear of the vehicle or to goods or luggage compartment, after folding and restoring those seats to the seating position, the safety-belts provided for those seats shall be accessible for use or can be easily recovered from under or behind the seat, by one person, according to instructions in the vehicle users handbook, without the need for that person to have training or practice. |
8.2.2.5. |
The Technical Service shall verify that, with the buckle tongue engaged in the buckle:
|
8.3. Special requirements for rigid parts incorporated in safety-belts or restraint systems
8.3.1. Rigid parts, such as the buckles, adjusting devices and attachments, shall not increase the risk of bodily injury to the wearer or to other occupants of the vehicle in the event of an accident.
8.3.2. The device for releasing the buckle shall be clearly visible to the wearer and within his easy reach and shall be so designed that it cannot be opened inadvertently or accidentally. The buckle shall also be located in such a position that it is readily accessible to a rescuer needing to release the wearer in an emergency.
The buckle shall be so installed that, both when not under load and when sustaining the wearer's mass, it is capable of being released by the wearer with a single simple movement of either hand in one direction.
In the case of a safety-belts or restraint systems for front outboard seating positions, except if these are harness belts, the buckle shall also be capable of being locked in the same manner.
A check shall be made to ensure that, if the buckle is in contact with the wearer, the width of the contact surface is not less than 46 mm.
A check shall be made to ensure that, if the buckle is in contact with the wearer, the contact surface satisfies the requirements of paragraph 6.2.2.1 of this Regulation.
8.3.3. When the belt is being worn, it shall either adjust automatically to fit the wearer or be so designed that the manual adjusting device is readily accessible to the wearer when seated and is convenient and easy to use. It shall also be possible for it to be tightened with one hand to suit the build of the wearer and the position of the vehicle seat.
8.3.4. Safety-belts or restraint systems incorporating retractors shall be so installed that the retractors are able to operate correctly and stow the strap efficiently. In case of both a belt adjusting device and a flexible shoulder adjustment device for height, in at least their highest and their lowest position, checks shall be made that the retractor automatically adjusts the strap to the shoulder of the concerned wearer after buckling, as well as that the tongue-plate rolls up in case of an unbuckling.
8.3.5. In order to inform vehicle user(s) of the provisions made for the transport of children, vehicles of Categories M1, M2, M3 and N1 shall meet the information requirements of Annex 17. Any vehicle of Category M1 shall be equipped with ISOFIX positions, in accordance with the relevant prescriptions of Regulation No 14 or Regulation No 145.
The first ISOFIX position shall allow at least the installation of one out of the three forward-facing fixtures as defined in Appendix 2 of Annex 17; the second ISOFIX position shall allow at least the installation of one rear-facing fixture as defined in Appendix 2 of Annex 17. For this second ISOFIX position, in case where the installation of the rear-facing fixture is not possible on the second row of seats of the vehicle due to its design, the installation of one fixture is allowed in any position of the vehicle.
8.3.6. Any i-Size seating position shall allow the installation of the ISOFIX child restraint fixture ‘ISO/F2X’, ‘ISO/R2’, and the support leg installation assessment volume as defined in Appendix 2 of Annex 17, as well as the booster seat fixture ‘ISO/B2’ as defined in Appendix 5 of Annex 17, without the ISOFIX attachments (see detail B). It shall be possible to occupy all adjacent i-Size seating positions simultaneously. This is deemed to be demonstrated when the vertical median planes of individual adjacent positions are at least 440 mm apart.
8.4. Safety-belt reminder equipment
8.4.1. Requirements per specific seating position and exemptions
8.4.1.1. The seating position of the driver of M and N categories of vehicles (9) as well as the seating positions of the occupants of seats in the same row as the driver seat of M and N categories of vehicles shall be equipped with a safety-belt reminder satisfying the requirements of paragraph 8.4.3.
8.4.1.2. All seating positions of the rear seat row(s) of M1 and N1 category vehicles (9) shall be equipped with a safety-belt reminder satisfying the requirements of paragraph 8.4.4.
Where the vehicle manufacturer provides a safety-belt reminder system on a rear seating position in another category of vehicle, the safety-belt reminder system may be approved according to this Regulation.
8.4.1.3. A safety-belt reminder is not compulsory on folding seats (i.e. normally folded and designed for occasional use, e.g. foldable crew seats in the buses and coaches) as well as seating positions fitted with an S-type belt (including Harness belt).
Notwithstanding paragraphs 8.4.1.1 and 8.4.1.2 above, safety belt reminders are also not required for rear seats in ambulances, hearses, and motor-caravans as well as for all seats for vehicles used for transport of disabled persons, vehicles intended for use by the armed services, civil defence, fire services and forces responsible for maintaining public order.
8.4.2. General requirements
8.4.2.1. Visual warning
8.4.2.1.1. The visual warning shall be so located as to be readily visible and recognisable in the daylight and at night time by the driver and distinguishable from other alerts.
8.4.2.1.2. The visual warning shall be a steady or flashing tell-tale.
8.4.2.2. Audible warning
8.4.2.2.1. The audible warning shall consist of a continuous or an intermittent (pauses shall not exceed 1 second) sound signal or of continuous vocal information. Where vocal information is employed, the vehicle manufacturer shall ensure that the alert is able to employ the languages of the market into which the vehicle is intended to be placed.
8.4.2.2.2. The audible warning shall be easily recognised by the driver.
8.4.2.3. First level warning
8.4.2.3.1. The first level warning shall be at least a visual warning activated for 30 seconds or longer for seating positions covered by paragraph 8.4.1.1 and for 60 seconds or longer for seating positions covered by paragraph 8.4.1.2 when the safety-belt of any of the seats is not fastened and the ignition switch or master control switch is activated.
8.4.2.3.2. The first level warning may be discontinued when:
(i) |
None of the safety-belts which triggered the warning are unfastened; or |
(ii) |
The seat or seats which triggered the warning are no longer occupied. |
8.4.2.3.3. The activation of the first level warning shall be tested according to the test procedure defined in Annex 18, paragraph 1.
8.4.2.4. Second level warning
8.4.2.4.1. The second level warning shall be a visual and audible signal activated for at least 30 seconds not counting periods in which the warning may stops for up to 3 seconds when at least one or any combination of the conditions at the choice of manufacturer, set out in paragraphs 8.4.2.4.1.1 to 8.4.2.4.1.3 is/are fulfilled. The second level warning shall supersede the first level warning when the first level warning is still active.
8.4.2.4.1.1. The distance driven greater than the distance threshold. The threshold shall not exceed 500 m. The distance driven when the vehicle is not in normal operation shall be excluded.
8.4.2.4.1.2. The vehicle speed greater than the speed threshold. The threshold shall not exceed 25 km/h.
8.4.2.4.1.3. The duration time (engine running, propulsion system activated, etc.) is greater than the duration time threshold. The threshold shall not exceed 60 seconds. The first level warning duration time and the duration time when the vehicle is not in normal operation shall be excluded.
8.4.2.4.2. The thresholds to trigger safety belt reminder listed in paragraphs 8.4.2.4.1.1 to 8.4.2.4.1.3, may be reset when:
(i) |
Any of the doors have been opened while the vehicle is not in normal operation; or |
(ii) |
The seat or seats which triggered the warning are no longer occupied. |
8.4.2.4.3. The second level warning may be discontinued when
(i) |
None of the safety-belts which triggered the warning are unfastened; |
(ii) |
The vehicle ceases to be in normal operation; or |
(iii) |
The seat or seats which triggered the warning are no longer occupied. |
8.4.2.4.4. The second level warning shall be resumed for the remainder of the required duration when one or any combination of the conditions, at the choice of the manufacturer, set out in paragraphs 8.4.2.4.1.1 to 8.4.2.4.1.3 is/are again fulfilled.
8.4.2.4.5. For the condition that a safety belt becomes unfastened pursuant to paragraphs 8.4.3.3 and 8.4.4.5, the thresholds set out in paragraphs 8.4.2.4.1.1 to 8.4.2.4.1.3 shall be measured from the point in time at which unfastening occurs.
8.4.2.4.6. The activation of the second level warning shall be tested according to the test procedure defined in Annex 18, paragraph 2.
8.4.3. Safety-belt reminder for driver and occupants of seats in the same row as the driver
8.4.3.1. Safety-belt reminders for driver and occupants of seats in the same row as the driver shall fulfil the requirements set out in paragraphs 8.4.2.
8.4.3.2. The colour and symbol of the visual warning shall be as defined in item 21 in Table 1 of Regulation No 121.
8.4.3.3. The second level warning shall be activated when a safety-belt is or becomes unfastened while the vehicle is in normal operation and while, at the same time, any one condition or any combination of the conditions, at the choice of the manufacturer, set out in paragraphs 8.4.2.4.1.1 to 8.4.2.4.1.3 is satisfied.
8.4.4. Safety-belt reminder for occupants of rear seat row(s).
8.4.4.1. Safety-belt reminders for occupants of rear row(s) shall fulfil the requirements set out in paragraphs 8.4.2.
8.4.4.2. The visual warning shall indicate at least all rear seating positions to allow the driver to identify, while facing forward as seated on the driver seat, any seating position in which the safety-belt is unfastened. For vehicles that have information on the occupancy status of the rear seats, the visual warning does not need to indicate unfastened safety-belts for unoccupied seating positions.
8.4.4.3. The colour of the visual warning may be other than red and the symbol of the visual warning for safety-belts covered by paragraph 8.4.1.2 may contain different symbols other than defined in Regulation No 121. In addition, the first level warning of seating positions covered by paragraph 8.4.1.2 may be cancellable by the driver.
8.4.4.4. A common tell-tale may be used for safety-belts covered by paragraphs 8.4.1.1 and 8.4.1.2.
8.4.4.5. The second level warning shall be activated when a safety-belt becomes unfastened while the vehicle is in normal operation and while, at the same time, any one condition or any combination of the conditions, at the choice of the manufacturer, set out in paragraphs 8.4.2.4.1.1 to 8.4.2.4.1.3 is satisfied.
8.4.5. The safety-belt reminder may be designed to allow deactivation.
8.4.5.1. In the case that a short-term deactivation is provided, it shall be significantly more difficult to deactivate the safety-belt reminder than buckling the safety-belt on and off (i.e. it shall consist of an operation of specific controls that are not integrated in the safety-belt buckle) and this operation shall only be possible when the vehicle is stationary. When the ignition or master control switch is deactivated for more than 30 minutes and activated again, a short-term deactivated safety-belt reminder shall reactivate. It shall not be possible to provide short-term deactivation of the relevant visual warning(s).
8.4.5.2. In the case that a facility for a long-term deactivation is provided, it shall require a sequence of operations to deactivate, that are detailed only in the manufacturer's technical manual and/or which requires the use of tools (mechanical, electrical, digital, etc.) that are not provided with the vehicle. It shall not be possible to provide long-term deactivation of the relevant visual warning(s).
9. CONFORMITY OF PRODUCTION
The conformity of production procedures shall comply with those set out in the Agreement, Appendix 2 (E/ECE/324-E/ECE/TRANS/505/Rev.2), with the following requirements:
9.1. Every vehicle type or safety-belt or restraint system approved under this Regulation shall be so manufactured as to conform to the type approved by meeting the requirements set forth in paragraphs 6, 7 and 8 above.
9.2. The minimum requirements for conformity of production control procedures set forth in Annex 14 to this Regulation shall be complied with.
9.3. The Type Approval Authority which has granted type approval may at any time verify the conformity control methods applied in each production facility. The normal frequency of these verifications shall be twice a year.
10. PENALTIES FOR NON-CONFORMITY OF PRODUCTION
10.1. The approval granted in respect of a vehicle or a type of belt or restraint system may be withdrawn if the requirement laid down in paragraph 9.1 above is not complied with, or if the safety-belt(s) or restraint system(s) selected have failed to pass the checks prescribed in paragraph 9.2 above.
10.2. If a Contracting Party to the Agreement applying this Regulation withdraws an approval it has previously granted, it shall forthwith so notify the other Contracting Parties applying this Regulation by means of a communication form conforming to the model in Annex 1A or Annex 1B to this Regulation (as appropriate).
11. MODIFICATIONS AND EXTENSION OF APPROVAL OF THE VEHICLE TYPE OR SAFETY-BELT OR RESTRAINT SYSTEM TYPE
11.1. Every modification of the vehicle type or the belt or restraint system or both shall be notified to the Type Approval Authority which approved the vehicle type or safety-belt or restraint system type. The Authority may then either:
11.1.1. |
Consider that the modifications made are unlikely to have an appreciable adverse effect and that in any case the vehicle or safety-belt or restraint system still complies with the requirements; or |
11.1.2. |
Require a further test report from the Technical Service responsible for conducting the tests. |
11.2. Without prejudice to the provisions of paragraph 11.1 above, a variant of the vehicle whose mass in the running order is less than that of the vehicle subjected to the approval test shall not be regarded as a modification of the vehicle type.
11.3. Confirmation or refusal of approval, specifying the alterations, shall be communicated by the procedure specified in paragraph 5.2.3 or 5.3.3 of this Regulation to the Parties to the Agreement applying this Regulation.
11.4. The Type Approval Authority issuing the extension of approval shall assign a series number for such an extension and inform thereof the other parties to the 1958 Agreement applying this Regulation by means of a communication form conforming to the model in Annex 1A or 1B to this Regulation.
12. PRODUCTION DEFINITIVELY DISCONTINUED
If the holder of the approval completely ceases to manufacture a device approved in accordance with this Regulation, he shall so inform the Type Approval Authority which granted the approval. Upon receiving the relevant communication that Authority shall inform thereof the other Parties to the 1958 Agreement applying this Regulation by means of a communication form conforming to the model in Annex 1A or 1B to this Regulation.
13. INSTRUCTIONS
In the case of safety-belt type supplied separately from vehicle, the packaging and installation instructions shall clearly state the vehicle type(s) for which it is intended.
14. NAMES AND ADDRESSES OF TECHNICAL SERVICES RESPONSIBLE FOR CONDUCTING APPROVAL TESTS AND OF TYPE APPROVAL AUTHORITIES
The Parties to the 1958 Agreement applying this Regulation shall communicate to the United Nations Secretariat the names and addresses of the Technical Services responsible for conducting approval tests and of the Type Approval Authorities which grant approval and to which forms certifying approval or refusal or extension or withdrawal of approval, issued in other countries, are to be sent.
15. TRANSITIONAL PROVISIONS
15.1. Approvals of vehicle type
15.1.1. As from the official date of entry into force of Supplement 15 to the 04 series of amendments, no Contracting Party applying this Regulation shall refuse to grant approvals under this Regulation as modified by Supplement 15 to the 04 series of amendments.
15.1.2. As from 2 years after the entry into force of Supplement 15 to the 04 series of amendments to this Regulation, Contracting Parties applying this Regulation shall grant approvals only if the requirements of this Regulation, as amended by Supplement 15 to the 04 series of amendments are satisfied.
15.1.3. As from 7 years after the entry into force of Supplement 15 to the 04 series of amendments to this Regulation, Contracting Parties applying this Regulation may refuse to recognise approvals which were not granted in accordance with Supplement 15 to the 04 series of amendments to this Regulation. However, existing approvals of the vehicle categories other than M1 and which are not affected by Supplement 15 to the 04 series of amendments to this Regulation shall remain valid and Contracting Parties applying this Regulation shall continue to accept them.
15.1.3.1. However, as from 1 October 2000, for vehicles of categories M1 and N1, Contracting Parties applying this Regulation may refuse to recognise approvals which were not granted in accordance with Supplement 8 to the 04 series of amendments to this Regulation, if the information requirements of paragraph 8.3.5 and Annex 17 are not met.
15.2. Installation of safety-belts and safety-belt reminder
These transitional provisions only apply to the installation of safety-belts and safety-belt reminders on vehicles and do not change the mark of the safety-belt.
15.2.1. As from the official date of entry into force of Supplement 12 to the 04 series of amendments, no Contracting Party applying this Regulation shall refuse to grant approvals under this Regulation as modified by Supplement 12 to the 04 series of amendments.
15.2.2. Upon expiration of a period of 36 months following the official date of entry into force referred to in paragraph 15.2.1 above, the Contracting Parties applying this Regulation shall grant approval only if the vehicle type satisfies the requirements of this Regulation as amended by the Supplement 12 to the 04 series of amendments.
15.2.3. Upon the expiration of a period of 60 months following the official date of entry into force referred to in paragraph 15.2.1 above, the Contracting Parties applying this Regulation may refuse to recognise approvals not granted in accordance with Supplement 12 to the 04 series of amendments to this Regulation.
15.2.4. As from the official date of entry into force of Supplement 14 to the 04 series of amendments, no Contracting Party applying this Regulation shall refuse to grant approvals under this Regulation as modified by Supplement 14 to the 04 series of amendments.
15.2.5. As from the official date of entry into force of Supplement 16 to the 04 series of amendments, no Contracting Party applying this Regulation shall refuse to grant approvals under this Regulation as modified by Supplement 16 to the 04 series of amendments.
15.2.6. Upon expiration of a period of 36 months following the official date of entry into force referred to in paragraph 15.2.4 above, the Contracting Parties applying this Regulation shall grant approval only if the vehicle type satisfies the requirements of this Regulation as amended by the Supplement 14 to the 04 series of amendments.
15.2.7. Upon the expiration of a period of 60 months following the official date of entry into force referred to in paragraph 15.2.4 above, the Contracting Parties applying this Regulation may refuse to recognise approvals not granted in accordance with Supplement 14 to the 04 series of amendments to this Regulation.
15.2.8. After 16 July 2006, the Contracting Parties applying this Regulation shall grant approval only if the vehicle type satisfies the requirements of this Regulation as amended by the Supplement 16 to the 04 series of amendments.
15.2.9. After 16 July 2008, the Contracting Parties applying this Regulation may refuse to recognise approvals to vehicles of category N1 not granted in accordance with Supplement 16 to the 04 series of amendments to this Regulation.
15.2.10. As from the official date of entry into force of the 05 series of amendments, no Contracting Party applying this Regulation shall refuse to grant approvals under this Regulation as amended by the 05 series of amendments.
15.2.11. As from 18 months after the date of entry into force, Contracting Party applying this Regulation shall grant approvals only if the vehicle type to be approved meets the requirements of this Regulation as amended by the 05 series of amendments.
15.2.12. As from 72 months after the date of entry into force of the 05 series of amendments to this Regulation, approvals to this Regulation shall cease to be valid, except in the case of vehicle types which comply with the requirements of this Regulation as amended by the 05 series of amendments.
15.2.13. Notwithstanding paragraph 15.2.12, approvals of the vehicle categories other than M1 to the preceding series of amendments to the Regulation which are not affected by the 05 series of amendments related to the requirements concerning the fitting of safety-belt reminders shall remain valid and Contracting Parties applying the Regulation shall continue to accept them.
15.2.14. Notwithstanding paragraph 15.2.12, approvals of the vehicle categories other than N2 and N3 to the preceding series of amendments to the Regulation which are not affected by the 05 series of amendments related to minimum requirements for safety-belts and retractors in Annex 16 shall remain valid and Contracting Parties applying the Regulation shall continue to accept them.
15.2.15. Even after the date of entry into force of the 05 series of amendments, approvals of the components and separate technical units to the preceding series of amendments to the regulation shall remain valid and Contracting Parties applying the regulation shall continue to accept them and shall not refuse to grant extensions of approval to the 04 series of amendments to this Regulation.
15.2.16. Notwithstanding the transitional provisions above, Contracting Parties whose application of this Regulation comes into force after the date of entry into force of the 05 series of amendments are not obliged to accept approvals which were granted in accordance with any of the preceding series of amendments to this Regulation.
15.3. As from the official date of entry into force of the 06 series of amendments, no Contracting Party applying this Regulation shall refuse to grant approvals under this Regulation as amended by the 06 series of amendments.
15.3.1. As from 24 months after the date of entry into force of the 06 series of amendments, Contracting Parties applying this Regulation shall grant approvals only if the requirements of this Regulation, as amended by the 06 series of amendments, are satisfied.
15.3.2. As from 36 months after the date of entry into force of the 06 series of amendments, Contracting Parties applying this Regulation may refuse to recognise approvals which were not granted in accordance with the 06 series of amendments to this Regulation.
15.3.3. Even after the date of entry into force of the 06 series of amendments, approvals of the components and separate technical units to the preceding series of amendments to the Regulation shall remain valid and Contracting Parties applying the Regulation shall continue to accept them, and Contracting Parties may continue to grant extensions of approvals to the 05 series of amendments.
15.3.4. Notwithstanding paragraphs 15.3.1 and 15.3.2, approvals of the vehicle categories to the preceding series of amendments to the Regulation which are not affected by the 06 series of amendments shall remain valid and Contracting Parties applying the Regulation shall continue to accept them.
15.3.5. As long as there are no requirements concerning the compulsory fitting of safety belts for folding seats in their national requirements at the time of acceding to this Regulation, Contracting Parties may continue to allow this non-fitment for the purpose of national approval and in this case these bus categories cannot be type approved under this Regulation.
15.3.6. No Contracting Parties applying this Regulation shall refuse to grant approvals of a component under a preceding series of amendments to the Regulation if the safety-belts are intended to be installed in vehicles which are approved before the respective series of amendment.
15.3.7. As from the official date of entry into force of Supplement 5 to the 06 series of amendments, no Contracting Party applying this Regulation shall refuse to grant type approvals under this Regulation as amended by Supplement 5 to the 06 series of amendments.
15.3.8. Until 12 months after the date of entry into force of the Supplement 5 to the 06 series of amendments to this Regulation, Contracting Parties applying this Regulation can continue to grant type approvals to the 06 series of amendments to this Regulation without taking into account the provisions of Supplement 5 to the 06 series of amendments.
15.3.9. Until 1 September 2018, no Contracting Parties applying this Regulation shall refuse to grant type approvals to the 06 series of amendments without taking into account Supplement 9 to the 06 series of amendments
15.4 As from the official date of entry into force of the 07 series of amendments, no Contracting Party applying this Regulation shall refuse to grant or refuse to accept type approvals under this Regulation as amended by the 07 series of amendments. Contracting Parties shall continue to grant extensions of approvals to the preceding series of amendment.
15.4.1 As from 1 September 2019, Contracting Parties applying this Regulation shall not be obliged to accept type approvals to the preceding series of amendments that were first issued on or after 1 September 2019.
15.4.2. A safety-belt reminder is not compulsory on removable rear seats and on any seat in a row in which there is a suspension seat, for the purpose of granting type-approval to the 07 series of amendment, until 1 September 2022. These exemptions shall remain applicable in the case of extensions of approvals first granted before 1 September 2022.
15.4.3 Until 1 September 2021, Contracting Parties applying this Regulation shall accept type approvals to the preceding series of amendments that were first issued before 1 September 2019.
15.4.4 As from 1 September 2021, Contracting Parties applying this Regulation shall not be obliged to accept type approvals issued to the preceding series of amendments to this Regulation.
15.4.5. Notwithstanding paragraph 15.4.4, Contracting Parties applying the Regulation shall continue to accept UN type approvals of safety-belts and restraint systems to the preceding series of amendments to the Regulation.
15.4.6. Notwithstanding paragraph 15.4.4, Contracting Parties applying the Regulation shall continue to accept type approvals to the preceding series of amendments to the Regulation, for vehicles which are not affected by the changes introduced by the 07 series of amendments.
(1) As defined in the Consolidated Resolution on the Construction of Vehicles (R.E.3.), document ECE/TRANS/WP.29/78/Rev.3, para. 2 - www.unece.org/trans/main/wp29/wp29wgs/wp29gen/wp29resolutions.html
(2) As defined in the Consolidated Resolution on the Construction of Vehicles (R.E.3.), document ECE/TRANS/WP.29/78/Rev.3, para. 2 - www.unece.org/trans/main/wp29/wp29wgs/wp29gen/wp29resolutions.html
(3) The distinguishing numbers of the Contracting Parties to the 1958 Agreement are reproduced in Annex 3 to the Consolidated Resolution on the Construction of Vehicles (R.E.3), document ECE/TRANS/WP.29/78/Rev. 3, Annex 3 - www.unece.org/trans/main/wp29/wp29wgs/wp29gen/wp29resolutions.html
(4) See the footnote to paragraph 5.2.4.1 of this Regulation.
(5) g = 9,81 m/s.
(6) The test has not been performed for woven straps in twill construction with high-tenacity polyester yarns as those webbings get wider under load. In that case the width without load shall be ≥ 46 mm.
(*1) See paragraph 7.4.1.6.4.3 below
(7) g = 9,81 m/s
(8) As defined in the Consolidated Resolution on the Construction of Vehicles (R.E.3.), document ECE/TRANS/WP.29/78/Rev.3, para. 2 - www.unece.org/trans/main/wp29/wp29wgs/wp29gen/wp29resolutions.html
(9) As defined in the Consolidated Resolution on the Construction of Vehicles (R.E.3.), document ECE/TRANS/WP.29/78/Rev.4, para. 2 - www.unece.org/trans/main/wp29/wp29wgs/wp29gen/wp29resolutions.html
ANNEX 2
ARRANGEMENTS OF THE APPROVAL MARKS
1. Arrangements of the vehicle approval marks concerning the installation of safety-belts
MODEL A
(See paragraph 5.2.4 of this Regulation)
The above approval mark affixed to a vehicle shows that the vehicle type concerned has, with regard to safety-belts, been approved in the Netherlands (E 4) pursuant to Regulation No 16. The approval number indicates that the approval was granted according to the requirements of Regulation No 16 as amended by the 07 series of amendments.
MODEL B
(See paragraph 5.2.5 of this Regulation)
The above approval mark affixed to a vehicle shows that the vehicle type concerned has been approved in the Netherlands (E 4) pursuant to Regulations Nos 16 and 52 (1). The approval numbers indicate that, at the dates when the respective approvals were given, Regulation No 16 included the 07 series of amendments and Regulation No 52 the 01 series of amendments.
2. Arrangements of the safety-belt approval marks (see paragraph 5.3.5 of this Regulation)
The belt bearing the above approval mark is a three-point belt (‘A’), fitted with an energy absorber (‘e’) and approved in the Netherlands (E 4) under the number 062439, the Regulation already incorporating the 06 series of amendments at the time of approval.
The belt bearing the above approval mark is a lap belt (‘B’), fitted with a retractor, type 4, with multiple sensitivity (m) and approved in the Netherlands (E 4) under the number 062489, the Regulation already incorporating the 06 series of amendments at the time of approval.
Note: The approval number and additional symbol(s) shall be placed close to the circle and either above or below the ‘E’ or to left or right of that letter. The digits of the approval number shall be on the same side of the ‘E’ and orientated in the same direction. The additional symbol(s) shall be diametrically opposite the approval number. The use of roman numerals as approval numbers should be avoided so as to prevent any confusion with other symbols.
The belt bearing the above approval mark is a special type belt (‘S’), fitted with an energy absorber (‘e’) and approved in the Netherlands (E 4) under the number 0622439, the Regulation already incorporating the 06 series of amendments at the time of approval.
The belt bearing the above approval mark is part of a restraint system (‘Z’), it is a special type belt (‘S’) fitted with an energy absorber (‘e’). It has been approved in the Netherlands (E 4) under the number 0624391, the Regulation already incorporating the 06 series of amendments at the time of approval.
The belt bearing this type approval mark is a three-point belt (‘A’) with a multiple-sensitivity (‘m’) type 4N (‘r4N’) retractor, in respect of which type approval was granted in the Netherlands (‘E 4’) under number 062439, the Regulation already incorporating the 06 series of amendments at the time of approval. This belt shall not be fitted to vehicles of category M1.
The safety-belt bearing this type approval mark is a three-point belt (‘A’) fitted with an energy absorber (‘e’), approved as meeting the specific requirements of paragraph 6.4.1.3.3 or 6.4.1.3.4 of this Regulation, and with a multiple-sensitivity (‘m’) type 4 (‘r4’) retractor, in respect of which type approval was granted in the Netherlands (‘E 4’) under the approval number 062439. The first two digits indicate that the Regulation already incorporated the 06 series of amendments at the time of the approval. This safety-belt has to be fitted to a vehicle equipped with an airbag in the given seating position.
(1) The second number is given merely as an example.
ANNEX 3
DIAGRAM OF AN APPARATUS TO TEST DURABILITY OF RETRACTOR MECHANISM
ANNEX 4
DIAGRAM OF AN APPARATUS TO TEST LOCKING OF EMERGENCY LOCKING RETRACTORS
A suitable apparatus is illustrated in the figure and consists of a motor-driven cam, the follower of which is attached by wires to a small trolley mounted on a track. The cam design and motor speed combination is such as to give the required acceleration at a rate of increase of acceleration as specified in paragraph 7.6.2.2 of this Regulation and the stroke is arranged to be in excess of the maximum permitted webbing movement before locking.
On the trolley a carrier is mounted which can be swivelled to enable the retractor to be mounted in varying positions relative to the direction of movement of the trolley.
When testing retractors for sensitivity to strap movement the retractor is mounted on a suitable fixed bracket and the strap is attached to the trolley.
When carrying out the above tests any brackets, etc. supplied by the manufacturer or his accredited representative shall be incorporated in the test installation to simulate as closely as possible the intended installation in a vehicle.
Any additional brackets, etc. that may be required to simulate the installation as intended in the vehicle shall be provided by the manufacturer or his accredited representative.
ANNEX 5
DIAGRAM OF AN APPARATUS FOR DUST-RESISTANCE TEST
(dimensions in millimetres)
ANNEX 6
DESCRIPTION OF TROLLEY, SEAT, ANCHORAGES AND STOPPING DEVICE
1. TROLLEY
For tests on safety-belts the trolley, carrying the seat only, shall have a mass of 400 ± 20 kg. For tests on restraint systems the trolley with the attached vehicle structure shall have a mass of 800 kg. However, if necessary, the total mass of the trolley and vehicle structure may be increased by increments of 200 kg. In no case shall the total mass differ from the nominal value by more than ± 40 kg.
2. SEAT
Except in the case of tests on restraint systems, the seat shall be of rigid construction and present a smooth surface. The particulars given in Figure 1 of this annex shall be respected, care being taken that no metal part can come into contact with the belt.
3. ANCHORAGES
3.1. In the case of a belt equipped with a belt adjustment device for height as defined in paragraph 2.14.6 of this Regulation, this device shall be secured either to a rigid frame, or to a part of the vehicle on which it is normally mounted which shall be securely fixed on the test trolley.
3.2. The general anchorages shall be positioned as shown in Figure 1. The marks which correspond to the arrangement of the anchorages show where the ends of the belt are to be connected to the trolley or to the load transducer, as the case may be. The anchorages for normal use are the points A, B and K if the strap length between the upper edge of the buckle and the hole for attachment of the strap support is not more than 250 mm. Otherwise, the points A1 and B1 shall be used. The tolerance on the position of the anchorage points is such that each anchorage point shall be situated at most at 50 mm from corresponding points A, B and K indicated in Figure 1 or A1, B1 and K, as the case may be.
3.3. The structure carrying the anchorages shall be rigid. The upper anchorage shall not be displaced by more than 0,2 mm in the longitudinal direction when a load of 98 daN is applied to it in that direction. The trolley shall be so constructed that no permanent deformation shall occur in the parts bearing the anchorages during the test.
3.4. If a fourth anchorage is necessary to attach the retractor, this anchorage:
|
Shall be located in the vertical longitudinal plane passing through K; |
|
Shall enable the retractor to be tilted to the angle prescribed by the manufacturer; |
|
Shall be located on the arc of a circle with radius KB1 = 790 mm if the length between the upper strap guide and the strap outlet at the retractor is not less than 540 mm or, in all other cases, on the arc of a circle with centre K and radius 350 mm. |
4. STOPPING DEVICE
4.1. The device consists of two identical absorbers mounted in parallel, except in the case of restraint systems when four absorbers shall be used for a nominal mass of 800 kg. If necessary, an additional absorber shall be used for each 200 kg increase of nominal mass. Each absorber comprises:
|
An outer casing formed from a steel tube; |
|
A polyurethane energy-absorber tube; |
|
A polished-steel olive-shaped knob penetrating into the absorber; and |
|
A shaft and an impact plate. |
4.2. The dimensions of the various parts of this absorber are shown in the diagrams reproduced in Figures 2, 3 and 4.
4.3. The characteristics of the absorbing material are given in the table of this annex. Immediately before each test the tubes shall be conditioned at a temperature between 15 °C and 25 °C for at least 12 hours without being used. During the dynamic testing of safety-belts or restraint systems, the stopping device shall be at the same temperature as during the calibration test, with a tolerance of ± 2 °C. The requirements to be met by the stopping device are given in Annex 8 to this Regulation. Any other device giving equivalent results may be used.
Characteristics of the absorbing material
(ASTM Method D 735 unless otherwise stated)
Shore hardness A |
95 ± 2 at 20 ± 5 °C temperature |
Breaking strength |
Ro > 343 daN/cm2 |
Minimum elongation |
Ao > 400 per cent |
Module at 100 per cent elongation |
> 108 daN/cm2 |
At 300 per cent elongation |
> 235 daN/cm2 |
Low-temperature brittleness (ASTM Method D 736) |
5 hours at – 55 °C |
Compression set (Method B) |
22 hours at 70 °C < 45 per cent |
Density at 25 °C |
between 1,05 and 1,10 |
Ageing in air (ASTM Method D 573) |
||||
70 hours at 100 °C |
|
max variation ±3 |
||
|
decrease < 10 per cent of Ro |
|||
|
decrease < 10 per cent of Ao |
|||
|
decrease < 1 per cent |
|||
Immersion in oil (ASTM Method No 1 Oil) |
||||
70 hours at 100 °C |
|
max variation ±4 |
||
|
decrease < 15 per cent of Ro |
|||
|
decrease < 10 per cent of Ao |
|||
|
swelling < 5 per cent |
|||
Immersion in oil (ASTM Method No 3 Oil) |
||||
70 hours at 100 °C |
|
decrease < 15 per cent of Ro |
||
|
decrease < 15 per cent of Ao |
|||
|
swelling < 20 per cent |
|||
Immersion in distilled water |
||||
1 week at 70 °C |
|
decrease < 35 per cent of Ro |
||
|
increase < 20 per cent of Ao |
Figure 1
Trolley, seat, anchorage

Figure 2
Stopping device
(Assembled)

Figure 3
Stopping device
(Polyurethane tube)

Figure 4
Stopping device
(Olive-shaped knob)
* |
This dimension can vary between 43 and 49 mm Dimensions in mm |
Surface finish
|
Interference tolerance ± 0,1 |
ANNEX 7
DESCRIPTION OF MANIKIN
1. SPECIFICATIONS OF THE MANIKIN
1.1. General
The main characteristics of the manikin are illustrated in the following figures and tables:
Figure 1 |
Side view of head, neck and torso; |
||||
Figure 2 |
Front view of head, neck and torso; |
||||
Figure 3 |
Side view of hip, thighs and lower leg; |
||||
Figure 4 |
Front view of hip, thighs and lower leg; |
||||
Figure 5 |
Principal dimensions; |
||||
Figure 6 |
Manikin in sitting position, showing:
|
||||
Table 1 |
References, names, materials and principal dimensions of components of the manikin; and |
||||
Table 2 |
Masses of head, neck, torso, thighs and lower leg. |
1.2. Description of the manikin
1.2.1. Structure of the lower leg (see Figures 3 and 4)
The structure of the lower leg consists of three components:
|
A sole plate (30); |
|
A shin tube (29); and |
|
A knee tube (26). |
The knee tube has two lugs which limit the movement of the lower leg in relation to the thigh.
The lower leg can be rotated rearwards 120° from the straight position.
1.2.2. Structure of the thigh (see Figures 3 and 4)
The structure of the thigh consists of three components:
|
Knee tube (22); |
|
A thigh bar (21); and |
|
A hip tube (20). |
Movement of the knee is limited by two cut-outs in the knee tube (22) which engage with the lugs of the lower leg.
1.2.3. Structure of the torso (see Figures 1 and 2)
The structure of the torso consists of:
|
A hip tube (2); |
|
A roller chain (4); |
|
Ribs (6) and (7); |
|
A sternum (8); and |
|
Chain attachments (3) and at parts (7) and (8). |
1.2.4. Neck (see Figures 1 and 2)
The neck consists of seven polyurethane discs (9). The stiffness of the neck can be adjusted by means of a chain tensioner.
1.2.5. Head (see Figures 1 and 2)
The head (15) itself is hollow; the polyurethane form is reinforced by steel plate (17). The chain tensioner by which the neck can be adjusted consists of a polyamide block (10), a tubular spacer (11), and tensioning members (12) and (13). The head can be turned about the Atlas-Axis joint, which consists of the adjuster assembly (14) and (18), the spacer (16) and polyamide block (10).
1.2.6. Knee joint (see Figure 4)
The lower leg and thighs are connected by a tube (27) and a tensioner (28).
1.2.7. Hip joint (see Figure 4)
The thighs and torso are connected by a tube (23), friction plates (24), and tensioner assembly (25).
1.2.8. Polyurethane
Type: PU 123 CH Compound
Hardness: 50-60 Shore A
1.2.9. Overalls
The manikin is covered by a special overall (see Table 1).
2. CORRECTION DEVICES
2.1. General
In order to calibrate the manikin to certain values and its total mass, the mass distribution are adjusted by the use of six correction steel masses of 1 kg each, which can be mounted at the hip joint. Six polyurethane weights each of 1 kg mass can be mounted in the back of the torso.
3. CUSHION
A cushion shall be positioned between the chest of the manikin and the overall. This cushion shall be made of polyethylene foam of the following specification:
Hardness: 7-10 Shore A
Thickness: 25 mm + 5
It shall be replaceable.
4. ADJUSTMENT OF THE JOINTS
4.1. General
In order to achieve reproducible results, it is necessary to specify and control the friction at each joint.
4.2. Knee joint
Tighten the knee joint.
Set the thigh and lower leg vertical.
Rotate the lower leg through 30°.
Gradually slacken the tensioner (28) until the lower leg starts to fall under its own mass.
Lock the tensioner in this position.
4.3. Hip joint
Tighten the hip joint.
Place the thigh in a horizontal position and the torso in a vertical position.
Rotate the torso in a forward direction until the angle between the torso and the thigh is 60°.
Gradually slacken the tensioner until the torso starts to fall under its own mass.
Lock the tensioner in this position.
4.4. Atlas-Axis joint
Adjust the Atlas-Axis joint so that it just resists its own weight in the fore and aft directions.
4.5. Neck
The neck can be adjusted by means of the chain tensioner (13). When the neck is adjusted, the upper end of the tensioner shall displace between 4-6 cm when subjected to a horizontal load of 10 daN.
Table 1
Reference No |
Name |
Material |
Dimensions |
1 |
Body material |
Polyurethane |
— |
2 |
Hip tube |
Steel |
76 × 70 × 100 mm |
3 |
Chain attachments |
Steel |
25 × 10 × 70 mm |
4 |
Roller chain |
Steel |
3/4 |
5 |
Shoulder plate |
Polyurethane |
— |
6 |
Rolled section |
Steel |
30 × 30 × 3 × 250 mm |
7 |
Ribs |
Perforated steel plate |
400 × 85 × 1,5 mm |
8 |
Sternum |
Perforated steel plate |
250 × 90 × 1,5 mm |
9 |
Discs (six) |
Polyurethane |
ø 90 × 20 mm |
|
|
|
ø 80 × 20 mm |
|
|
|
ø 75 × 20 mm |
|
|
|
ø 70 × 20 mm |
|
|
|
ø 65 × 20 mm |
|
|
|
ø 60 × 20 mm |
10 |
Block |
Polyamide |
60 × 60 × 25 mm |
11 |
Tubular spacer |
Steel |
40 × 40 × 2 × 50 mm |
12 |
Tensioning bolt |
Steel |
M16 × 90 mm |
13 |
Tensioner nut |
Steel |
M16 |
14 |
Tensioner for Atlas-Axis joint |
Steel |
ø 12 × 130 mm (M12) |
15 |
Head |
Polyurethane |
— |
16 |
Tubular spacer |
Steel |
ø 18 × 13 × 17 mm |
17 |
Reinforcement plate |
Steel |
30 × 3 × 500 mm |
18 |
Tensioner nut |
Steel |
M12 mm |
19 |
Thighs |
Polyurethane |
— |
20 |
Hip tube |
Steel |
76 × 70 × 80 mm |
21 |
Thigh bar |
Steel |
30 × 30 × 440 mm |
22 |
Knee tube |
Steel |
52 × 46 × 40 mm |
23 |
Hip connection tube |
Steel |
70 × 64 × 250 mm |
24 |
Friction plates (four) |
Steel |
160 × 75 × 1 mm |
25 |
Tensioner assembly |
Steel |
M12 × 320 mm + Plates and nuts |
26 |
Knee tube |
Steel |
52 × 46 × 160 mm |
27 |
Knee connection tube |
Steel |
44 × 39 × 190 mm |
28 |
Tensioner plate |
Steel |
ø 70 × 4 mm |
29 |
Shin tube |
Steel |
50 × 50 × 2 × 460 mm |
30 |
Sole plate |
Steel |
100 × 170 × 3 mm |
31 |
Torso correction mass (six) |
Polyurethane |
Each mass 1 kg |
32 |
Cushion |
Polyethylene foam |
350 × 250 × 25 mm |
33 |
Overall |
Cotton and polyamide straps |
— |
34 |
Hip correction masses (six) |
Steel |
Each mass 1 kg |
Table 2
Components of manikin |
Mass in kg |
Head and neck |
4,6 ± 0,3 |
Torso and arms |
40,3 ± 1,0 |
Thighs |
16,2 ± 0,5 |
Lower leg and foot |
9,0 ± 0,5 |
Total mass including correction weights |
75,5 ± 1,0 |
Figure 1
Figure 2
Figure 3 |
Figure 4 |
|
|
Figure 5
Figure 6
G= centre of gravity
T= torso reference point (at the rear on the centre line of the manikin)
P= pelvis reference point (at the rear on the centre line of the manikin)
The displacement measurement at point P shall not contain rotational components around the hip axis and around a vertical axis.
ANNEX 8
DESCRIPTION OF CURVE OF TROLLEY'S DECELERATION OR ACCELERATION AS A FUNCTION OF TIME
In all cases the calibration and measuring procedures shall correspond to those defined in the International Standard ISO 6487 (2002); the measuring equipment shall correspond to the specification of a data channel with a channel frequency class (CFC) 60.
Definition of the different curves
Time (ms) |
Acceleration (g) Low corridor |
Acceleration (g) High corridor |
0 |
— |
20 |
10 |
0 |
— |
10 |
15 |
— |
15 |
20 |
— |
18 |
— |
32 |
25 |
26 |
— |
45 |
26 |
— |
55 |
20 |
— |
60 |
0 |
32 |
80 |
— |
0 |

The additional segment (see paragraph 7.7.4.2) applies only for the acceleration sled.
ANNEX 9
INSTRUCTIONS
Every safety-belt shall be accompanied by instructions of the following content or kind in the language or languages of the country in which it is to be placed on sale:
1. |
Installation instructions (not required if the vehicle manufacturer is to install the safety-belt) which specify for which vehicle models the assembly is suitable and the correct method of attachment of the assembly to the vehicle, including a warning to guard against chafing of the straps. |
2. |
User instructions (may be included in the vehicle user's handbook if the safety-belt is installed by the vehicle manufacturer) which specify the instructions to ensure that the user obtains the greatest benefit from the safety-belt. In these instructions reference shall be made to:
|
3. |
In the case of safety-belts fitted with a type 4N retractor, it shall be indicated in the installation instructions and on any packaging that this belt is not suitable for installation in motor vehicles used for the carriage of passengers having not more than nine seats, including that of the driver. |
4. |
An installation requirement for the consumer shall be provided by the manufacturer/applicant for all vehicles where the crotch strap assembly can be used. The manufacturer of the harness belt shall prescribe the mounting of the additional reinforcement elements for the anchorages of crotch straps and their installation in all vehicles where an installation is provided for. |
ANNEX 11
ABRASION AND MICRO-SLIP TEST
Figure 1
Type I procedure
Examples of test arrangements corresponding to the type of adjusting device
EXAMPLE A

EXAMPLE B

Figure 2
Type 2 procedure


Figure 3
Type 3 procedure and micro-slip test
Total travel: 300 ± 20 mm

The load of 5 daN on the testing device shall be vertically guided in such a way as to avoid load-swing and twisting of the strap.
The attaching device shall be fixed to the load of 5 daN in the same manner as in a vehicle.
ANNEX 12
CORROSION TEST
1. TEST APPARATUS
1.1. The apparatus shall consist of a mist chamber, a salt solution reservoir, a supply of suitably conditioned compressed air, one or more atomising nozzles, sample supports, provision for heating the chamber, and necessary means of control. The size and detail construction of the apparatus shall be optional, provided that the test conditions are met.
1.2. It is important to ensure that drops of solution accumulated on the ceiling or cover of the chamber do not fall on test samples.
1.3. Drops of solution which fall from test samples shall not return to the reservoir for respraying.
1.4. The apparatus shall not be constructed of materials that will affect the corrosiveness of the mist.
2. LOCATION OF TEST SAMPLES IN THE MIST CABINET
2.1. Samples, except retractors, shall be supported or suspended between 15° and 30° from the vertical and preferably parallel to the principal direction of horizontal flow of mist through the chamber, based upon the dominant surface being tested.
2.2. Retractors shall be supported or suspended so that the axes of the reel for storing the strap shall be normal to the principal direction of horizontal flow of mist through the chamber. The strap opening in the retractor shall also be facing in this principal direction.
2.3. Each sample shall be placed so as to permit free setting of mist on all samples.
2.4. Each sample shall be so placed as to prevent salt solution from one sample dripping on to any other sample.
3. SALT SOLUTION
3.1. The salt solution shall be prepared by dissolving 5 ± 1 parts by mass of sodium chloride in 95 parts of distilled water. The salt shall be sodium chloride substantially free of nickel and copper and containing on the dry basis not more than 0,1 per cent of sodium iodide and not more than 0,3 per cent of total impurities.
3.2. The solution shall be such that when atomised at 35 °C the collected solution is in the pH range of 6,5 to 7,2.
4. AIR SUPPLY
The compressed air supply to the nozzle or nozzles for atomising the salt solution shall be free of oil and dirt, and maintained at a pressure between 70 kN/m2 and 170 kN/m2.
5. CONDITIONS IN THE MIST CHAMBER
5.1. The exposure zone of the mist chamber shall be maintained at 35 ± 5 °C. At least two clean mist collectors shall be placed within the exposure zone so that no drops of solution from the test samples or any other sources are collected. The collectors shall be placed near the test samples, one nearest to any nozzle and one furthest from all nozzles. The mist shall be such that for each 80 cm2 of horizontal collecting areas, there is collected in each collector from 1,0 to 2,0 ml of solution per hour when measured over an average of at least 16 hours.
5.2. The nozzle or nozzles shall be directed or baffled so that the spray does not impinge directly on test samples.
ANNEX 13
ORDER OF TESTS
Paragraphs |
Test |
Samples |
|||||||||||||||
Belt or restraint system No |
Strap No |
||||||||||||||||
1 |
2 |
3 |
4 |
5 |
1 |
2 |
3 |
4 |
5 |
6 |
7 |
8 |
9 |
10 |
11 |
||
4./6.1.2./6.1.3./6.2.1.1./6.2.2./6.2.3.1./6.3.1.1. |
Inspection of belt or restraint system |
X |
|
|
|
|
|
|
|
|
|
|
|
|
|
|
|
2.21./2.22./6.2.2.2. |
Inspection of buckle |
X |
X |
X |
X |
X |
|
|
|
|
|
|
|
|
|
|
|
6.2.2.6./6.2.2.7./ 7.5.1./7.5.5. |
Buckle strength test |
|
|
X |
|
|
|
|
|
|
|
|
|
|
|
|
|
6.2.3.3./7.5.1. |
Strength test on adjusting device (and where necessary retractors) |
|
|
X |
|
|
|
|
|
|
|
|
|
|
|
|
|
6.2.4./7.5.2. |
Strength test on attachments (and where necessary on retractors) |
|
|
X |
|
|
|
|
|
|
|
|
|
|
|
|
|
6.2.2.3./7.5.3. |
Low-temperature test on buckle |
X |
X |
|
|
|
|
|
|
|
|
|
|
|
|
|
|
6.2.1.4./7.5.4. |
Low-temperature impact test on rigid parts |
X |
X |
|
|
|
|
|
|
|
|
|
|
|
|
|
|
6.2.3.2./6.2.3.4./7.5.6. |
Ease of adjustment |
|
|
|
X |
|
|
|
|
|
|
|
|
|
|
|
|
|
Conditioning/ testing of belt or restraint system before dynamic test |
|
|
|
|
|
|
|
|
|
|
|
|
|
|
|
|
6.2.2.4. |
Durability of buckle |
X |
X |
|
|
|
|
|
|
|
|
|
|
|
|
|
|
6.2.1.2./7.2. |
Corrosion resistance of rigid parts |
X |
X |
|
|
|
|
|
|
|
|
|
|
|
|
|
|
|
Conditioning of retractors |
|
|
|
|
|
|
|
|
|
|
|
|
|
|
|
|
6.2.5.2.1./6.2.5.3.1./6.2.5.3.3./7.6.2. |
Locking threshold |
X |
X |
|
|
|
|
|
|
|
|
|
|
|
|
|
|
6.2.5.2.2./6.2.5.3.4./7.6.4. |
Retracting force |
X |
X |
|
|
|
|
|
|
|
|
|
|
|
|
|
|
6.2.5.2.3./6.2.5.3.3./7.6.1. |
Durability |
X |
X |
|
|
|
|
|
|
|
|
|
|
|
|
|
|
6.2.5.2.3./6.2.5.3.3./7.2. |
Corrosion |
X |
X |
|
|
|
|
|
|
|
|
|
|
|
|
|
|
6.2.5.2.3./6.2.5.3.3./7.6.3. |
Dust |
X |
X |
|
|
|
|
|
|
|
|
|
|
|
|
|
|
6.3.1.2./7.4.3. |
Testing of strap width |
|
|
|
|
|
X |
X |
|
|
|
|
|
|
|
|
|
|
Strap strength test after |
|
|
|
|
|
|
|
|
|
|
|
|
|
|
|
|
6.3.2./7.4.1.1./7.4.2. |
Room conditioning |
|
|
|
|
|
X |
X |
|
|
|
|
|
|
|
|
|
6.3.3./7.4.1.2./7.4.2. |
Light conditioning |
|
|
|
|
|
|
|
X |
X |
|
|
|
|
|
|
|
6.3.3./7.4.1.3./7.4.2. |
Low-temperature conditioning |
|
|
|
|
|
|
|
|
|
X |
X |
|
|
|
|
|
6.3.3./7.4.1.4./7.4.2. |
Heat conditioning |
|
|
|
|
|
|
|
|
|
|
|
X |
X |
|
|
|
6.3.3./7.4.1.5./7.4.2. |
Water conditioning |
|
|
|
|
|
|
|
|
|
|
|
|
|
X |
X |
|
6.2.3.2./7.3. |
Micro-slip test |
|
|
|
X |
X |
|
|
|
|
|
|
|
|
|
|
|
6.4.2./7.4.1.6. |
Abrasion test |
|
|
|
X |
X |
|
|
|
|
|
|
|
|
|
|
|
6.4.1./7.7. |
Dynamic test |
X |
X |
|
|
|
|
|
|
|
|
|
|
|
|
|
|
6.2.2.5./6.2.2.7./7.8. |
Buckle-opening test |
X |
X |
|
|
|
|
|
|
|
|
|
|
|
|
|
|
7.1.4. |
Retention of strap sample |
|
|
|
|
|
|
|
|
|
|
|
|
|
|
|
X |
ANNEX 14
CONTROL OF CONFORMITY OF PRODUCTION
1. TESTS
Safety-belts shall be required to demonstrate compliance with the requirements on which the following tests are based:
1.1. Verification of the locking threshold and durability of emergency locking retractors
According to the provisions of paragraph 7.6.2 of this Regulation in the most unfavourable direction as appropriate after having undergone the durability testing detailed in paragraphs 7.2, 7.6.1 and 7.6.3 as a requirement of paragraph 6.2.5.3.5 of this Regulation.
1.2. Verification of the durability of automatically-locking retractors
According to the provisions of paragraph 7.6.1 of this Regulation supplemented by the tests in paragraphs 7.2 and 7.6.3 as a requirement of paragraph 6.2.5.2.3 of this Regulation.
1.3. Test for strength of straps after conditioning
According to the procedure described in paragraph 7.4.2 of this Regulation after conditioning according to the requirements of paragraph 7.4.1.1 to 7.4.1.5 of this Regulation.
1.3.1. Test for strength of straps after abrasion
According to the procedure described in paragraph 7.4.2 of this Regulation after conditioning according to the requirements described in paragraph 7.4.1.6 of this Regulation.
1.4. Micro-slip test
According to the procedure described in paragraph 7.3 of this Regulation.
1.5. Test of the rigid parts
According to the procedure described in paragraph 7.5 of this Regulation.
1.6. Verification of the performance requirements of the safety-belt or restraint system when subjected to the dynamic test
1.6.1. Tests with conditioning
1.6.1.1. Belts or restraint systems fitted with an emergency locking retractor according to the provisions set out in paragraphs 7.7 and 7.8 of this Regulation, using a belt which has previously been subjected to 45 000 cycles of the endurance test of the retractor prescribed in paragraph 7.6.1 of this Regulation and to the tests defined in paragraphs 6.2.2.4, 7.2 and 7.6.3 of this Regulation.
1.6.1.2. Belts or restraint systems fitted with an automatically-locking retractor: according to the provisions set out in paragraphs 7.7 and 7.8 of this Regulation, using a belt which has previously been subjected to 10 000 cycles of the endurance test of the retractor prescribed in paragraph 7.6.1 and also to the tests prescribed in paragraphs 6.2.2.4, 7.2 and 7.6.3 of this Regulation.
1.6.1.3. Static belts: according to the provisions set out in paragraphs 7.7 and 7.8 of this Regulation, on a safety-belt which has been subjected to the test prescribed in paragraphs 6.2.2.4 and 7.2 of this Regulation.
1.6.2. Test without any conditioning
According to the provisions set out in paragraphs 7.7 and 7.8 of this Regulation.
2. TEST FREQUENCY AND RESULTS
2.1. The frequency of testing to the requirements of paragraphs 1.1 to 1.5 of this annex shall be on a statistically controlled and random basis in accordance with one of the regular quality assurance procedures.
2.1.1. Furthermore, in the case of emergency locking retractors, all assemblies shall be checked:
2.1.1.1. |
Either according to the provisions set out in paragraphs 7.6.2.1 and 7.6.2.2 of this Regulation, in the most unfavourable direction as specified in paragraph 7.6.2.1.2. Test results shall meet the requirements of paragraphs 6.2.5.3.1.1 and 6.2.5.3.3 of this Regulation. |
2.1.1.2. |
Or according to the provisions set out in paragraph 7.6.2.3 of this Regulation, in the most unfavourable direction. Nevertheless, the speed of inclination can be more than the prescribed speed insofar as it does not affect the test results. Test results shall meet the requirements of paragraph 6.2.5.3.1.4 of this Regulation. |
2.2. In the case of compliance with the dynamic test according to paragraph 1.6 of this annex, this shall be carried out with a minimum frequency of:
2.2.1. Tests with conditioning
2.2.1.1. In the case of belts fitted with an emergency locking retractor,
Where the daily production is greater than 1 000 belts: one in 100 000 belts produced, with a minimum frequency of one every two weeks,
Where the daily production is smaller than or equal to 1 000 belts: one in 10 000 belts produced, with a minimum frequency of one per year, per sort of locking mechanism (1),
Shall be subjected to the test prescribed in paragraph 1.6.1.1 of this annex.
2.2.1.2. In the case of belts fitted with an automatically-locking retractor and of static belts,
Where the daily production is greater than 1 000 belts: one in 100 000 belts produced, with a minimum frequency of one every two weeks,
Where the daily production is smaller than or equal to 1 000 belts: one in 10 000 belts produced, with a minimum frequency of one per year,
Shall be subjected to the test prescribed in paragraphs 1.6.1.2 or 1.6.1.3 of this annex respectively.
2.2.2. Tests without conditioning
2.2.2.1. In the case of belts fitted with an emergency locking retractor, the following number of samples shall be subject to the test prescribed in paragraph 1.6.2 above:
2.2.2.1.1. For a production of not less than 5 000 belts per day, two belts per 25 000 produced with a minimum frequency of one per day, per sort of locking mechanism;
2.2.2.1.2. For a production of less than 5 000 belts per day, one belt per 5 000 produced with a minimum frequency of one per year, per sort of locking mechanism;
2.2.2.2. In the case of belts fitted with an automatically-locking retractor and of static belts, the following number of samples shall be subjected to the test prescribed in paragraph 1.6.2 above;
2.2.2.2.1. For a production of not less than 5 000 belts per day, two belts per 25 000 produced with a minimum of one per day, per approved type;
2.2.2.2.2. For a production of less than 5 000 belts per day, one belt per 5 000 produced with a minimum frequency of one per year, per approved type;
2.2.3. Results
Test results shall meet the requirements set out in paragraph 6.4.1.3.1 of this Regulation.
The forward displacement of the manikin may be controlled with regard to paragraph 6.4.1.3.2 of this Regulation (or 6.4.1.4 where applicable) during a test performed by means of a simplified adapted method.
A simplified, adapted method could be, e.g. the use of a reference chest speed measured at 300 mm forward displacement carried out in a physical test without an airbag or additional restraint system components, to be considered in the conformity control plan.
2.2.3.1. In the case of approval following paragraph 6.4.1.3.3 or 6.4.1.3.4 of this Regulation and paragraph 1.6.1 of this annex, it is only specified that no part of the belt shall be destructed or disengaged, and that a speed of 24 km/h of the chest reference point at 300 mm displacement shall not be exceeded.
2.3. Where a test sample fails a particular test to which it has been subjected, a further test to the same requirements shall be carried out on at least three other samples. In the case of dynamic tests, if one of the latter fails the test, the holder of the approval or his duly accredited representative shall notify the Type Approval Authority which has granted type approval indicating what steps have been taken to re-establish the conformity of production.
(1) For the purposes of this annex, ‘sort of locking mechanism’ means all emergency locking retractors whose mechanisms differ only in the lead angle(s) of the sensing device to the vehicle's reference axis system.
ANNEX 15
Procedure for determining the ‘H’ point and the actual torso angle for seating positions in motor vehicles (1)
Appendix 1 — |
Description of the three dimensional ‘H’ point machine (1) |
Appendix 2 — |
Three-dimensional reference system (1) |
Appendix 3 — |
Reference data concerning seating positions (1) |
(1) The procedure is described in Annex 1 and its Appendices 1, 2 and 3 to the Consolidated Resolution on the Construction of Vehicles (R.E.3) (document ECE/TRANS/WP.29/78/Rev.3 - www.unece.org/trans/main/wp29/wp29wgs/wp29gen/wp29resolutions.html
ANNEX 16
SAFETY-BELT INSTALLATION SHOWING THE BELT TYPES AND RETRACTOR TYPES
Minimum requirements for safety-belts and Retractors |
||||||
Vehicle category |
Forward facing seating positions |
Rearward-facing seating positions |
Side-facing seating position |
|||
Outboard seating positions |
Centre seating position |
|||||
Front |
Other than front |
Front |
Other than front |
|||
M1 |
Ar4m |
Ar4m |
Ar4m |
Ar4m |
B, Br3, Br4m |
— |
M2 < 3,5 t |
Ar4m, Ar4Nm |
Ar4m, Ar4Nm |
Ar4m, Ar4Nm |
Ar4m, Ar4Nm |
Br3, Br4m, Br4Nm |
— |
M2 > 3,5 t |
Br3, Br4m, Br4Nm, or Ar4m or Ar4Nm ߦ |
Br3, Br4m, Br4Nm, or Ar4m or Ar4Nm ߦ |
Br3, Br4m, Br4Nm or Ar4m or Ar4Nm ߦ |
Br3, Br4m, Br4Nm or Ar4m or Ar4Nm ߦ |
Br3, Br4m, Br4Nm |
— |
M3 |
Br3, Br4m, Br4Nm, or Ar4m or Ar4Nm ߦ See para. 8.1.7 for conditions when a lap belt is permitted |
Br3, Br4m, Br4Nm, or Ar4m or Ar4Nm ߦ See para. 8.1.7 for conditions when a lap belt is permitted |
Br3, Br4m, Br4Nm or Ar4m or Ar4Nm ߦ See para. 8.1.7 for conditions when a lap belt is permitted |
Br3, Br4m, Br4Nm or Ar4m or Ar4Nm ߦ See para. 8.1.7 for conditions when a lap belt is permitted |
— |
B, Br3, Br4m, Br4Nm |
N1 |
Ar4m, Ar4Nm |
Ar4m, Ar4Nm, Br4m, Br4Nm Ø |
B, Br3, Br4m, Br4Nm or A, Ar4m, Ar4Nm* (1) |
B, Br3, Br4m, Br4Nm |
B, Br3, Br4m, Br4Nm |
— |
Para. 8.1.2.1 lap belt permitted if seat is inboard of a passageway |
Para. 8.1.6 lap belt permitted if the windscreen is not in the reference zone |
|||||
N2 |
Br3, Br4m, Br4Nm orAr4m, Ar4Nm* Para. 8.1.6 lap belt permitted if the windscreen is outside the reference zone and for the driver's seat |
B, Br3, Br4m, Br4Nm |
B, Br3, Br4m, Br4Nm, or A, Ar4m, Ar4Nm* Para. 8.1.6 lap belt permitted if the windscreen is not in the reference zone |
B, Br3, Br4m, Br4Nm |
B, Br3, Br4m, Br4Nm |
— |
N3 |
Br3, Br4m, Br4Nm orAr4m, Ar4Nm* Para. 8.1.6 lap belt permitted if the windscreen is outside the reference zone and for the driver's seat |
B, Br3, Br4m, Br4Nm |
B, Br3, Br4m, Br4Nm, or A, Ar4m, Ar4Nm* Para. 8.1.6 lap belt permitted if the windscreen is not in the reference zone |
B, Br3, Br4m, Br4Nm |
B, Br3, Br4m, Br4Nm |
— |
|
|
|
|
|
|
|
A: three-point (lap and diagonal) belt |
B: 2-point (lap) belt |
r: retractor |
m: emergency locking retractor with multiple sensitivity |
|||
3: automatically locking retractor |
4: emergency locking retractor |
N: higher response threshold |
(see Regulation No 16, paras. 2.14.3 and 2.14.5) |
|||
*: Refers to para. 8.1.6 of this Regulation (2) |
Ø: Refers to para. 8.1.2.1 of this Regulation |
ߦ: Refers to para. 8.1.7 of this Regulation (2) |
|
Note: In all cases all S-type belts may be fitted in place of all possible A or B type belts, provided their anchorages comply with Regulation No 14.
Where a harness belt has been approved as a S-type belt according to this Regulation, using the lap belt strap, the shoulder belt straps and possibly one or more retractors, one or two additional crotch straps including their attachments for their anchorages may be provided by the manufacturer/applicant. These additional anchorages need not meet the requirements of Regulation No 14 (Erratum to Supplement 14 to the 04 series of amendments, applicable ‘ab initio.’).
(1) Erratum to Supplement 12 to the 04 series of amendments, applicable ‘ab initio.’
(2) Erratum to Revision 4, applicable ‘ab initio.’
ANNEX 17
Requirements for the installation of safety-belts and restraint systems for adult occupants of power-driven vehicles on forward facing seats, for the installation of ISOFIX child restraint systems and i-Size child restraint systems
1. COMPATIBILITY WITH CHILD RESTRAINT SYSTEMS
1.1. The vehicle manufacturer shall include in the vehicle handbook, simple advice to the vehicle user on the suitability of each passenger seating position for the fitting of child restraint systems. This information shall be given by pictograms or in the national language, or at least one of the national languages, of the country in which the vehicle is offered for sale.
For each forward-facing passenger seating position, and for each specified ISOFIX position, the vehicle manufacturer shall indicate:
(a) |
If the seating position is suitable for child restraints of the ‘universal’ category (see paragraph 1.2 below); and/or |
(b) |
If the seating position is suitable for i-Size child restraint systems (see paragraph 1.4 below); and/or |
(c) |
If the seating position is suitable for child restraint systems other than those specified above (e.g. see paragraph 1.3 below). |
If a seating position is only suitable for use with forward-facing child restraint systems, this shall also be indicated in the vehicle handbook.
In addition to the above information for the vehicle user, the vehicle manufacturers shall make available the information as defined by Appendix 3 of this Annex. For example, this information can be included in separate Annexes of the vehicle handbook, or in technical descriptions of the vehicle or on a dedicated webpage. The location to access this information shall be provided in the vehicle handbook.
1.2. A child restraint system of the universal category means a child restraint approved to the ‘universal’ category of Regulation No 44, Supplement 5 to 03 series of amendments (or subsequent amendments). Positions, which are indicated by the vehicle manufacturer as being suitable for the installation of child restraint systems of the universal category shall comply with the provisions of Appendix 1 and Appendix 5 to this annex.
1.3. An ISOFIX child restraint means a child restraint approved to Regulation No 44, Supplement 5 to 03 series of amendments or to Regulation No 129 (or subsequent amendments). Positions, which are indicated by the vehicle manufacturer as being suitable for the installation of ISOFIX child restraint systems shall comply with the provisions of Appendix 2 to this annex.
1.4. An i-Size child restraint means a child restraint approved to the i-Size category of Regulation No 129. Seating positions, which are indicated by the vehicle manufacturer as being suitable for the installation of i-Size child restraint systems shall comply with the provisions of Appendix 2 and Appendix 5 to this annex.
APPENDIX 1
Provisions concerning the installation of ‘universal’ category child restraint systems installed with the safety-belt equipment of the vehicle
1. GENERAL
1.1. The test procedure and the requirements in this appendix shall be used to determine the suitability of seating positions for the installation of child restraints of the ‘universal’ category.
1.2. The tests may be carried out in the vehicle or in a representative part of the vehicle.
2. TEST PROCEDURE
2.1. Adjust the seat to its fully rearward and lowest position.
2.2. Adjust the seat-back angle to the manufacturer's design position. In the absence of any specification, an angle of 25 degrees from the vertical, or the nearest fixed position of the seat-back, should be used.
2.3. Set the shoulder anchorage to the lowest position.
2.4. Place a cotton cloth on the seat-back and cushion.
2.5. Place the fixture (as described in Figure 1 of this appendix) on the vehicle seat.
2.6. If the seating position is intended to accommodate a forward-facing or rearward-facing universal restraint system, proceed according to paragraphs 2.6.1, 2.7, 2.8, 2.9 and 2.10 below. If the seating position is intended to accommodate only a forward-facing universal restraint system, proceed according to paragraphs 2.6.2, 2.7, 2.8, 2.9 and 2.10 below.
2.6.1. Arrange the safety-belt strap around the fixture in approximately the correct position as shown in Figures 2 and 3, then latch the buckle.
2.6.2. Arrange the safety-belt lap strap approximately in the correct position around the lower part of the fixture of 150 mm radius as shown in Figure 3, then latch the buckle.
2.7. Ensure that the fixture is located with its vertical plane of symmetry within ± 25 mm of the vertical plane of symmetry of the seating position.
2.8. Ensure that all webbing slack is removed. Use sufficient force to remove the slack, do not attempt to tension the webbing.
2.9. Push rearwards on the centre of the front of the fixture with a force of 100 N ± 10 N, applied parallel to the lower surface, and remove the force.
2.10. Push vertically downwards on the centre of the upper surface of the fixture with a force of 100 N ± 10 N, and remove the force.
3. REQUIREMENTS
3.1. The base of the fixture shall contact both the forward and rearward parts of the seat cushion surface. If such contact does not occur due to the belt access gap in the test fixture, this gap may be covered in line with the bottom surface of the test fixture.
3.2. The lap portion of the belt shall touch the fixture on both sides at the rear of the lap belt path (see Figure 3).
3.3. The lap portion of the belt shall touch the fixture on both sides at the rear of the lap belt path (see Figure 3). The seat belt webbing shall always cover the points BP on the left and right ends of the curved edge; the exact position of point BP on the curved edge is indicated in detail W of Figure 1.
Figure 1
Specifications of the fixture

Figure 2 Installation of fixture onto vehicle seat (see paragraph 2.6.1) |
Figure 3 Check for compatibility (see paragraphs 2.6.1 and 3.2) |
|
APPENDIX 2
Provisions concerning the installation of forward-facing and rearward-facing ISOFIX child restraint systems of universal and semi-universal categories installed on ISOFIX or i-Size positions
1. GENERAL
1.1. The test procedure and the requirements in this appendix shall be used to determine the suitability of ISOFIX positions for the installation of ISOFIX child restraint systems of universal and semi-universal categories, as well as to determine the suitability of i-Size seating positions for installing i-Size child restraint systems.
1.2. The tests may be carried out in the vehicle or in a representative part of the vehicle.
For i-Size seating positions, compliance with the i-Size support leg installation requirements may be assessed by a physical test, computer simulation or representative drawings.
2. TEST PROCEDURE
ISOFIX positions in the vehicle, defined by the vehicle manufacturer shall be checked to ensure that the CRF listed in paragraph 4 of this Appendix can be accommodated. Where the vehicle manufacturer has indicated that the ISOFIX position(s) will accommodate a particular CRF, then it shall be assumed that smaller CRFs of the same orientation may be accommodated.
i-Size seating positions, defined by the vehicle manufacturer, shall be checked to ensure that it is possible to accommodate both the ISO/R2 and the ISO/F2X child restraint fixtures (see paragraph 4 of this Annex) including the i-Size support leg installation assessment volume.
For both, ISOFIX and i-Size position(s), the following procedure shall apply:
2.1. |
When checking a CRF, on a seat, with or without i-Size support leg installation assessment volume, this seat may be adjusted longitudinally to its rearmost position and in its lowest position. |
2.2. |
Adjust the seat-back angle to the manufacturer's design position and the head restraint in the lowest and rearmost position. In the absence of any specification an angle of the seat-back corresponding to a torso angle of 25° from the vertical, or the nearest fixed position of the seat-back, shall be used. When checking a CRF, on a rear seat, with or without i-Size support leg installation assessment volume, the vehicle seat located in front of this rear seat may be adjusted longitudinally forward but not further than the mid-position between its rearmost and fore most positions. The seat backrest angle may also be adjusted, but not to a more upright angle than corresponding to a torso angle of 15°. |
2.3. |
Place cotton clothes on the seat-back and cushion, if needed. |
2.4. |
Place the CRF, with or without i-Size support leg installation assessment volume, on the ISOFIX or i-Size position. |
2.5. |
Push, towards ISOFIX anchorages system, on the centre between the ISOFIX anchorages with a force of 100 N ± 10 N, applied parallel to the lower surface, and remove the force. |
2.6. |
Attach the CRF, with or without i-Size support leg installation assessment volume, to the ISOFIX anchorages system. |
2.7. |
Push vertically downwards on the centre of the upper surface of the fixture with a force of 100 N ± 10 N, and remove the force. |
3. REQUIREMENTS
The following testing conditions only apply for the CRF(s), with or without i-Size support leg installation assessment volume, when accommodated in the ISOFIX and/or i-Size position. It is not required that the CRF(s), with or without i-Size support leg installation assessment volume, shall be able to move in and out of the ISOFIX and/or i-Size position under these conditions.
3.1. It has to be possible to accommodate the CRF(s), with or without i-Size support leg installation assessment volume, without interference with the vehicle interior. The CRF base shall have a pitch angle of 15° ± 10°, above the horizontal plane passing through the ISOFIX anchorages system. ISOFIX attachments, according to detail Y of figures 1 to 9, may adjust longitudinally between – 10 mm to + 70 mm to facilitate the interference check. The figures are showing the most extended positions.
3.2. The ISOFIX top tether anchorage, if any, shall remain accessible.
3.3. Should the above requirements not be met with the adjustments indicated in paragraph 2 above, the seats, the seat-backs, the head restraints may be adjusted to alternative positions designated by the manufacturer for normal use following which the above installation procedure shall be repeated and the requirements verified and met. These alternative positions shall be described in the vehicle handbook and with the additional information specified in Table 2 and/or 3 given in Appendix 3 to this annex. Passenger seats in front of i-Size seating positions may also be displaced to a position forward of the normal position of use. In such cases, the vehicle manufacturer shall provide information in the vehicle handbook, that the respective passenger seat shall not be occupied in such positions of displacement.
3.4 Should the above requirements not be fulfilled when some removable interior fittings were present, such fittings may be removed and then requirements of paragraph 3 have to be verified again and fulfilled. In such a case corresponding information shall be included in Table 2 and/or 3 of Appendix 3 of this annex.
4. ISOFIX CHILD RESTRAINT SYSTEM SIZE ENVELOPE FIXTURES
— |
ISO/F3: Full-Height Forward Facing toddler CRS |
— |
ISO/F2: Reduced-Height Forward Facing toddler CRS |
— |
ISO/F2X: Reduced-Height Forward Facing toddler CRS |
— |
ISO/R3: Full-Size Rearward Facing toddler CRS |
— |
ISO/R2: Reduced-Size Rearward Facing toddler CRS |
— |
ISO/R2X: Reduced-Size Rearward Facing toddler CRS |
— |
ISO/R1: Rearward Facing infant CRS |
— |
ISO/L1: Left Lateral Facing position CRS (carry-cot) |
— |
ISO/L2: Right Lateral Facing position CRS (carry-cot) |
The fixtures above shall be constructed with a mass between 10 and 13 kg +/– 1 kg and shall be of suitable durability and stiffness to satisfy the functional requirements, following the table below:
CRF |
Mass (kg) |
Tolerance (kg) |
R1 (1) |
10 |
± 1 |
R2/R2X (1) |
10 |
± 1 |
R3 |
13 |
± 1 |
L1/L2 |
13 |
± 1 |
F2/F2X (1) |
13 |
± 1 |
F3 |
13 |
± 1 |
4.1. Full-height forward-facing toddler child restraint systems envelope
Figure 1
ISO/F3 envelope dimensions for a full-height forward-facing toddler CRS (height 720 mm) ISOFIX SIZE CLASS A
Key
1 |
Limits in the forward and upwards directions. |
2 |
Dashed line marks area where a support leg, or similar, of a specific vehicle CRS is allowed to protrude. |
3 |
N/A. |
4 |
Further specifications of the connector area are given in Regulation No 44. |
4.2. Reduced-height forward-facing toddler child restraint systems envelope
Figure 2
ISO/F2 envelope dimensions for a reduced-height forward-facing toddler CRS, (height 650 mm) — ISOFIX SIZE CLASS B
Key
1 |
Limits in the forward and upwards directions. |
2 |
Dashed line marks area where a support leg, or similar, of a specific vehicle CRS is allowed to protrude. |
3 |
N/A. |
4 |
Further specifications of the connector area are given in Regulation No 44. |
5 |
Attachment point for the top tether strap. |
4.3. Reduced-height second version back shape forward-facing toddler child restraint systems envelope
Figure 3
ISO/F2X envelope dimensions for a reduced-height second version back surface shape forward-facing toddler CRS, (height 650 mm) — ISOFIX SIZE CLASS B1
Key
1 |
Limits in the forward and upwards directions. |
2 |
Dashed line marks area where a support leg, or similar, of a specific vehicle CRS is allowed to protrude. |
3 |
N/A. |
4 |
Further specifications of the connector area are given in Regulation No 44. |
4.4. Full-size rearward facing toddler child restraint system envelope
Figure 4
ISO/R3 envelope dimensions for a full-size rearward-facing toddler CRS ISOFIX SIZE CLASS C
Key
1 |
Limits in the rearward and upwards directions. |
2 |
Dashed line marks area where a support leg, or similar, of a specific vehicle CRS is allowed to protrude. |
3 |
The backwards limitation (to the right in the figure) is given by the forward-facing envelope in Figure 2. |
4 |
Further specifications of the connector area are given in Regulation No 44. |
4.5. Reduced-size rearward-facing toddler child restraint systems envelope
Figure 5
ISO/R2 envelope dimensions for a reduced-size rearward-facing toddler CRS ISOFIX SIZE CLASS D
Key
1 |
Limits in the rearward and upwards directions. |
2 |
Dashed line marks area where a support leg, or similar, of a specific vehicle CRS is allowed to protrude. |
3 |
The backwards limitation (to the right in the figure) is given by the forward-facing envelope in Figure 2. |
4 |
Further specifications of the connector area are given in Regulation No 44. |
4.6. Rearward facing infant child restraint systems envelope
Figure 6
ISO/R1 envelope dimensions for an infant-size rearward-facing CRS ISOFIX SIZE CLASS E
Key
1 |
Limits in the rearward and upwards directions. |
2 |
Dashed line marks area where a support leg, or similar, of a specific vehicle CRS is allowed to protrude. |
3 |
The backwards limitation (to the right in the figure) is given by the forward-facing envelope in Figure 2. |
4 |
Further specifications of the connector area are given in Regulation No 44. |
4.7. Rearward facing infant child restraint systems envelope ISO/R2X
Figure 7
Reduced-Size Rearward Facing toddler CRS Envelope dimensions for a reduced-size rearward-facing CRS, modified for improved compatibility with the vehicle interior
Key
1 |
Limits in the rearward and upward directions. |
2 |
Dashed lines mark the area where an anti-rotation device, or similar (e.g. rebound bar), is allowed to protrude. |
3 |
The backward limitation (to the right in the figure) is given by the forward-facing envelope in Figure 2. |
4 |
For further specifications of the connector area, see detail Y and ISO 13216-1:1999, Figures 2 and 3. |
4.8. Lateral facing child restraint systems envelope
Figure 8
Envelope dimensions for lateral facing position CRS — ISO/L1 — or symmetrically opposite — ISO/L2 (figure shown)
Note: The envelope for a left lateral-facing infant CRS (ISO/L1) has dimensions symmetric to ISO/L2 with regard to its intermediate longitudinal plan.
Key
1 |
Limits in the rearward and upward directions. |
2 |
Dashed lines mark the area where an anti-rotation device, or similar (e.g. rebound bar), is allowed to protrude. |
Figure 9
Side view of the i-Size support leg installation assessment volume for assessing compatibility of the i-Size seating positions with support legs of i-Size child restraint systems
Key:
1. |
Child Restraint Fixture (CRF). |
2. |
ISOFIX low anchorages bar. |
3. |
Plane formed by the bottom surface of the CRF when installed in the designated seating position. |
4. |
Plane passing through the lower anchorage bar and oriented perpendicular to the median longitudinal plane of the CRF and perpendicular to the plane formed by the bottom surface of the CRF when installed in the designated seating position. |
5. |
i-Size support leg installation assessment volume representing the geometrical boundaries for an i-Size child restraint system support leg. |
6. |
Vehicle floor. |
Note: Drawing not to scale.
Figure 10
3D view of the i-Size support leg installation assessment volume for assessing compatibility of the i-Size seating positions with support legs of i-Size child restraint systems
Key:
1. |
Child Restraint Fixture (CRF). |
2. |
ISOFIX low anchorages bar. |
3. |
Median longitudinal plane of the CRF. |
4. |
i-Size support leg installation assessment volume. |
Note: Drawing not to scale.
(1) ISOFIX base mass taken into account.
APPENDIX 3
EXAMPLE OF DETAILED INFORMATION E.G. FOR CHILD RESTRAINT SYSTEM MANUFACTURERS
This table gives technical information specifically intended e.g. for child restraint system manufacturer and as such translation into national languages is not required.
|
Seating position |
||||||||
Seat position number |
1 |
2 |
3 |
4 |
5 |
6 |
7 |
8 |
9 |
Seating position suitable for universal belted (yes/no) |
|
|
|
|
|
|
|
|
|
i-Size seating position (yes/no) |
|
|
|
|
|
|
|
|
|
Seating position suitable for lateral fixture (L1 L2) |
|
|
|
|
|
|
|
|
|
Largest suitable rearward facing fixture (R1/R2X/R2/R3) |
|
|
|
|
|
|
|
|
|
Largest suitable forward facing fixture (F1/F2X/F2 F3) |
|
|
|
|
|
|
|
|
|
Largest suitable booster fixture (B2/B3) |
|
|
|
|
|
|
|
|
|
1. |
Add information for each non i-Size seating position compatible with a support leg, as described in this regulation. |
2. |
Add information for each seating position equipped with lower ISOFIX anchorages but without Top Tether, according to this regulation. |
3. |
Add information if the adult safety belt buckles are located laterally in between both ISOFIX lower anchorages. |
Note:
1. |
Orientation is normal driving direction; columns for seating positions not available in a vehicle can be deleted. |
2. |
The numbering of seating positions shall be made on basis of following definition:
The information about the seat position number can be given by means of a table or by sketches or pictograms. |
APPENDIX 4
INSTALLATION OF 10-YEAR MANIKIN
(a) |
Adjust the seat to its fully rearward position. |
(b) |
Adjust the seat height in accordance with the manufacturer's specifications. In the absence of any specification, adjust the seat to the lowest position. |
(c) |
Adjust the seat back angle to the manufacturer's design position. In the absence of any specification, an angle of 25 degrees from the vertical, or the nearest fixed position of the seat back, should be used. |
(d) |
Set the shoulder anchorage to the lowest position. |
(e) |
Set the manikin on the seat ensuring that the pelvis is in contact with the seat back. |
(f) |
The longitudinal plan passing by the manikin centre line will be on the apparent centre line of the seating position. |
APPENDIX 5
Provisions concerning the installation of forward-facing booster seat child restraint systems of universal and specific categories installed on vehicle seating positions or i-Size seating positions
1. GENERAL
1.1. The test procedure and the requirements in this appendix shall be used to determine the suitability of seating positions for the installation of the booster seat fixtures ISO/B2 or ISO/B3, without ISOFIX attachments. Where the vehicle manufacturer has indicated that the vehicle position(s) will accommodate a particular CRF, then it shall be assumed that smaller CRFs of the same orientation will also be accommodated.
1.2. The tests may be carried out in the vehicle or in a representative part of the vehicle. Compliance with this requirement can be proven by a physical test or computer simulation or representative drawings.
2. TEST PROCEDURE
i-Size positions in the vehicle, defined by the vehicle manufacturer, shall be checked to ensure that the ISO/B2 fixture listed in paragraph 4 of this Appendix can be accommodated, at least without ISOFIX connections.
2.1. Adjust the seat to its fully rearward and lowest position.
2.2. Adjust the seat-back angle to the manufacturer's design position. In the absence of any specification, a torso angle of 25 degrees from the vertical, or the nearest fixed position of the seat-back, should be used.
2.3. When checking a CRF, on a rear seat, the vehicle seat located in front of this rear seat may be adjusted longitudinally forward but not further than the mid-position between its rearmost and fore most positions. The seat backrest angle may also be adjusted, but not to a more upright angle than corresponding to a torso angle of 15°. If the front seat is adjustable in height, adjust to the manufacturer's specification. In the absence of any specification, adjust the front seat to mid height position, or the nearest position to mid-height.
2.4. If necessary, head restraints may be adjusted or removed, if possible.
2.5. Set the shoulder anchorage to the position defined by the vehicle manufacturer.
2.6. Place cotton cloths on the seat-back and cushion, if needed.
2.7. Remove the ISOFIX attachments from the CRF, or retract them to a position fully inside the backseat line (reference line E, Figure 2 or 3).
2.8. Place the fixture (as described in Figure 2 or 3 of this appendix) on the vehicle seat. The top of the fixture may touch the vehicle roof. Compression of the seat cushion is allowed to move the fixture into position.
2.9. Arrange the seat belt through the CRF in approximately the correct position, and then fasten the buckle. Ensure that all webbing slack is removed. The fixture shall be restrained by the vehicle's seat belt.
2.10. Ensure that the fixture is located with its centreline on the apparent centreline of the seating position ± 25 mm with its centreline parallel with the centreline of the vehicle seat. The roll angle α (see figure 1) shall be within 0° ± 5°
2.11. Push rearwards on the centre of the front of the fixture with a force 100 N ± 10 N, applied parallel to the lower surface, and remove the force.
2.12. When possible, push vertically downwards on the centre of the upper surface of the fixture with a force of 100 N ± 10 N, and remove the force.
3. REQUIREMENTS
3.1. It shall be possible to secure the fixture in the seating position using the 3-point seat belt and to buckle up the seat belt.
3.2. The roll angle α as shown in Figure 1 shall be equal to or less than 5°.
3.3. The base of the fixture shall be in contact with the seat cushion, and the back face of the fixture shall be in contact with the seat back or head restraint. Full contact with the seat is not necessary, ‘gaps’ due to the vehicle seats contours are permitted as shown by the arrows in Figure 1. The booster seat envelope is equipped with an adjustable backrest. Compatibility with the vehicle seating position shall be achieved in at least one position of the backrest range shown in Figure 2 or Figure 3.
3.4. Should the above requirements not be met with the adjustments indicated in paragraphs 2.1 to 2.12 above, the seat, seat-back and safety-belt anchorages may be adjusted to an alternative position designated by the manufacturer for normal use at which the above installation procedure shall be repeated and the requirements again verified and met. This alternative position shall be described according to paragraph 1.1 of Annex 17 and in detailed technical information specified in Appendix 3.
4. BOOSTER SEAT CHILD RESTRAINT SYSTEM FIXTURES:
(a) |
ISO/B2: Booster seat, reduced width 440 mm (figure 2); |
(b) |
ISO/B3: booster seat, full width 520 mm (figure 3). |
The fixtures above shall be constructed with a mass of 7 kg +/– 1 kg and shall be of suitable durability and stiffness to satisfy the functional requirements.
Figure 1
Positioning in Seat
Figure 2
ISO/B2: Envelope dimensions for booster seat, reduced width 440 mm — without ISOFIX, or with connectors removed or stowed within the body of the fixture (behind line E, as defined by detail B)
Key
E is the reference axle of rotation of the backrest (90° to 110°) and reference line for retraction/stowing of ISOFIX.
Figure 3
ISO/B3 — Envelope dimensions for booster seat, full width 520 mm — without ISOFIX, or with connectors removed or stowed within the body of the fixture (behind line E, as defined by detail B)
Key
E is the reference axle of rotation of the backrest (90° to 110°) and reference line for retraction/stowing of ISOFIX.
ANNEX 18
SAFETY-BELT REMINDER TESTS
1. The first level warning shall be tested according to the following conditions:
(a) |
Safety-belt is not fastened; |
(b) |
Engine or propulsion system is stopped or idling, and the vehicle is not in forward or reverse motion; |
(c) |
Transmission is in neutral position; |
(d) |
Ignition switch or master control switch is activated; |
(e) |
A load of 40 kg is placed on each seat cushion in the same row as the driver's seat, or the state in which occupants are on board the vehicle is simulated by an alternative method specified by the vehicle manufacturer, provided an occupant's load does not exceed 40 kg. This may also be done for the rear seats at the request of the vehicle manufacturer. Or alternatively (at the choice of the manufacturer): An object or human representing a 5th percentile adult female (1) is placed on each seat cushion as specified by the manufacturer in the same row as the driver seat, or the state in which occupants are on board the vehicle is simulated by an alternative method specified by the vehicle manufacturer as agreed by the technical service and the approval authority. This may also be done for the rear seats at the request of the vehicle manufacturer; |
(f) |
The state of the safety-belt reminder is checked for all of the relevant seat(s), in conditions (a) to (e). |
2. The second level warning shall be tested according to the conditions set out in paragraphs 2.1 to 2.3 of this Annex, respectively.
2.1. Testing the driver's seating position
2.1.1. Testing the driver's seat when the safety-belt is unfastened before the journey
(a) |
The safety-belt of the driver's seat is not fastened; |
(b) |
The safety-belts of seats other than the driver's seat are fastened; |
(c) |
Test vehicle driven with one or any combination of the conditions of paragraphs 2.1.1.1 to 2.1.1.3 of this annex at the manufacturer's choice; |
(d) |
The state of the safety-belt reminder is checked for the driver's seat, in conditions (a) to (c). |
2.1.1.1. Accelerate the test vehicle to 25 – 0/+ 10 km/h from a halt and continue on the same speed.
2.1.1.2. The test vehicle is driven forward at least 500 m from a halt position.
2.1.1.3. The vehicle is tested when the vehicle is in normal operation for at least 60 seconds.
2.1.2. Testing the driver's seat when the safety-belt becomes unbuckled during the journey.
(a) |
The safety-belts of the driver's seat and seats other than the driver's seat are fastened; |
(b) |
The test vehicle is driven, at the choice of the manufacturer, under one of the conditions in paragraphs 2.1.1.1 to 2.1.1.3 of this annex or a combination thereof; |
(c) |
The safety-belt of the driver's seat is unbuckled. |
2.2. Testing the seating position(s) in the same row as the driver's seat
2.2.1. Testing the seat(s) in the same row as the driver's seat when the safety-belt is unfastened before the journey:
(a) |
The safety-belt(s) of the seat(s) in the same row as the driver's seat is/are not fastened; |
(b) |
The safety-belts of the seats other than the seat(s) in the same row as the driver's seat are fastened; |
(c) |
A load of 40 kg is applied to the seat(s) in the same row as the driver's seat, or the state in which occupants are on board the vehicle is simulated by a method specified by the manufacturer. Or alternatively (at the choice of the manufacturer): An object or human representing a 5th percentile adult female is placed on each seat cushion as specified by the manufacturer in the same row as the driver seat, or the state in which occupants are on board the vehicle is simulated by an alternative method specified by the vehicle manufacturer as agreed by the technical service and the approval authority. This may also be done for the rear seats at the request of the vehicle manufacturer; |
(d) |
The test vehicle is driven, at the choice of the manufacturer, under one of the conditions in paragraphs 2.1.1.1 to 2.1.1.3 of this annex or combination thereof; |
(e) |
The state of the safety-belt reminder is checked for all of the seat(s) in the same row as the driver's seat, in conditions (a) to (d). |
2.2.2. Testing the seating position in the same row as the driver's seat when the safety-belt becomes unbuckled during the journey.
(a) |
The safety-belts of the driver's seat and seats other than the driver's seat are fastened; |
(b) |
A load of 40 kg is applied to the seat(s) in the same row as the driver's seat, or the state in which occupants are on board the vehicle is simulated by a method specified by the manufacturer. Or alternatively (at the choice of the manufacturer): An object or human representing a 5th percentile adult female is placed on each seat cushion as specified by the manufacturer in the same row as the driver seat, or the state in which occupants are on board the vehicle is simulated by an alternative method specified by the vehicle manufacturer as agreed by the technical service and the approval authority. This may also be done for the rear seats at the request of the vehicle manufacturer; |
(c) |
The test vehicle is driven, at the choice of the manufacturer, under one of the conditions in paragraphs 2.1.1.1 to 2.1.1.3 of this annex or combination thereof; |
(d) |
The safety-belt(s) of the seats in the same row as the driver's seat is (are) unbuckled; |
(e) |
The state of the safety-belt reminder is checked for all of the seat(s) in the same row as the driver's seat, for each condition (a) to (d). |
2.3. Testing the rear seats
(a) |
With the test vehicle stationary, the safety-belts of all seats are fastened; |
(b) |
The test vehicle is put in normal operation and kept running; |
(c) |
The safety-belt of one of the rear seats is unfastened; |
(d) |
The functioning of the safety-belt reminder is checked for all of the seating positions in all seating rows; |
(e) |
Alternatively, at the request of the vehicle manufacturer, the test procedures specified in paragraphs 2.2 to 2.2.2 for the seating position(s) in the same row as the driver's seat may be used for any rear seating position instead. |
3. The first level warning test shall have a duration of at least the minimum required time as specified in paragraph 8.4.2.3 of this Regulation for the first level warning. The second level warning test may be initiated after completion of the first level warning test. However, it shall also be ensured that the second level warning supersedes the first level warning when the first level warning is still active.
(1) The technical specifications and detailed drawings of Hybrid III, corresponding to the principal dimensions of a fifth percentile female of the United States of America, and the specifications for its adjustment for this test are deposited with the Secretary-General of the United Nations and may be consulted on request at the secretariat of the Economic Commission for Europe, Palais des Nations, Geneva, Switzerland. A female who weighs between 46,7 and 51,25 kg, and who is between 139,7 and 150 cm tall may be used.
附件:
托管标准,您可以接收以下服务:
1 标准定期系统查新,若有最新版本,会以站内短信或邮件的形式通知用户;
2 随时在标准托管页面中查看到该条标准的最新状态;
3 若用户有在学习和科研中的需要,可以在标准托管页面中试阅标准;
4 企业如果需要上新产品,我院及时提供标准查询、采购等方面的支持;
5 为企业在标准制修订、企业良好行为创建以及标准化试点过程中遇到的困难,可联系我院指定相关专家负责进行指导帮助、提供政策咨询;
6 为企业提供标准化政策的解读、标准化知识的推广培训、标准自我公开声明、标准文献的免费查询、企业标准化体系建设等方面的标准化服务;
标准资讯点击排行榜 全部
资讯标题点击
[[ n.title ]] [[ n.read ]]大连标准化公共服务平台
版权:大连标准化研究院有限公司
地址:大连市中山区高原街56号
电话:0411-82740851
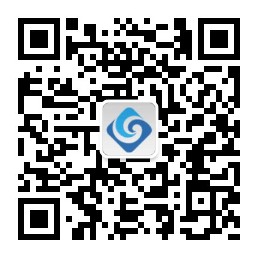